How does inFlow calculate the cost of a product/cost of goods sold?
If you’re using the Moving Average, FIFO, or LIFO costing method, you may be wondering how the program calculates your product’s unit cost when you purchase it from your vendor.
Web
inFlow calculates the cost of a product as it enters your inventory (via purchase or manufacture orders) based on several factors:
- Vendor unit price (including any discounts)
- Shipping fee/freight
- Non-vendor costs
- Service items on the purchase order
- Manufacturing (cost of components, operations, and other costs on manufacture orders)
inFlow does not include any taxes on the purchase order when calculating the cost.
We’ll use a sample purchase order to help explain the above cost factors in detail.
Vendor unit price
The purchase order displays the vendor unit price in the Unit Price column. If a product has a discount, it affects the Subtotal column on the order.
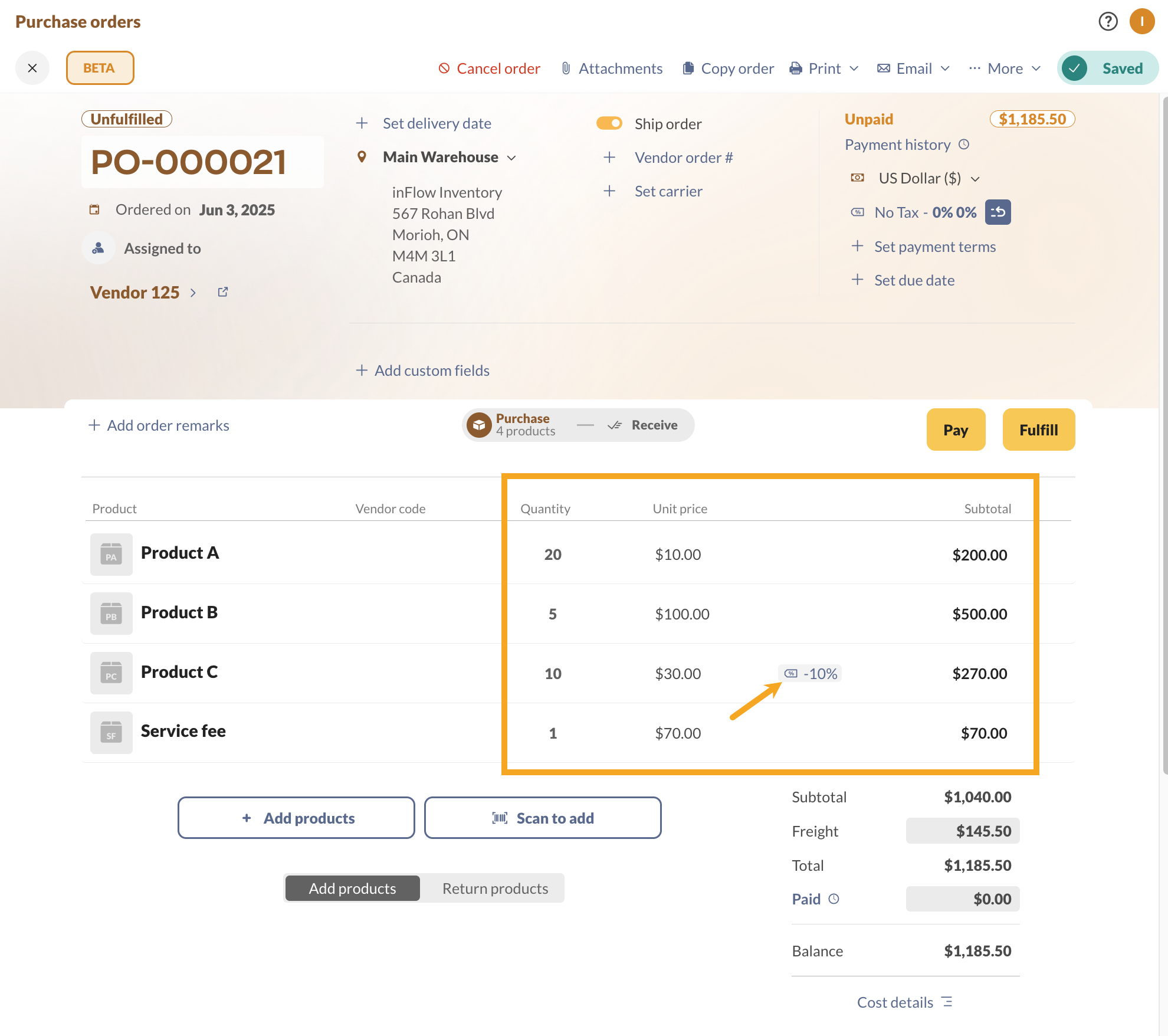
Calculating the unit price per product
Product Subtotal ÷ Product Quantity = Unit Price
Following the example purchase order above, you would get the following values:
Vendor Unit Price (incl. discount)
Product A: $200 ÷ 20 = $10
Product B: $500 ÷ 5 = $100
Product C: $270 ÷ 10 = $27
Reminder: Product C’s unit price isn’t $30 because the 10% discount applied.
Freight
If your vendor is charging you freight/shipping fees, you can enter the amount in the Freight field (above the order balance).
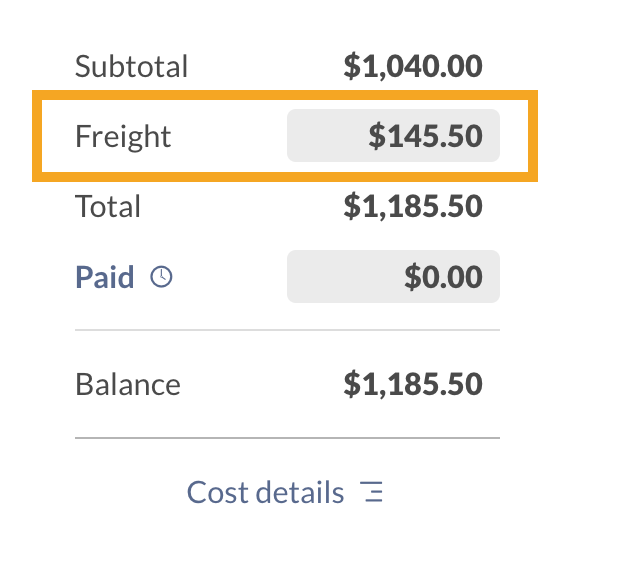
If you don’t see this field in your purchase order, toggle on Ship order at the top of the order.
inFlow takes the amount in the Freight field and distributes it across all stocked products on the purchase order. The Freight fee is spread over all stocked products and is weighted based on the unit price of each product.
To get the freight value for each product
Unit Price ÷ [Sum of Stocked Products subtotal] × Freight Total = Freight per unit
The subtotal of the stocked products on the order example is $970.00
Following the example purchase order above, you would get the following values:
Freight (unit)
- Product A: $10 ÷ $970 × $145.50 = $1.50
- Product B: $100 ÷ $970 × $145.50 = $15
- Product C: $27 ÷ $970 × $145.50 = $4.05
Non-vendor costs
If you need to pay any duties/ import fees/tariffs, you’ll need to record this under the Non-Vendor Cost field (bottom left of the purchase order). Only add charges to non-vendor costs for payments that aren’t directed to your vendor.
This distribution of non-vendor costs is weighted depending on the unit price of the product.
Any extra fees that you are required to pay your vendor should go in either the freight field or as a service fee on the order, not in non-vendor costs.
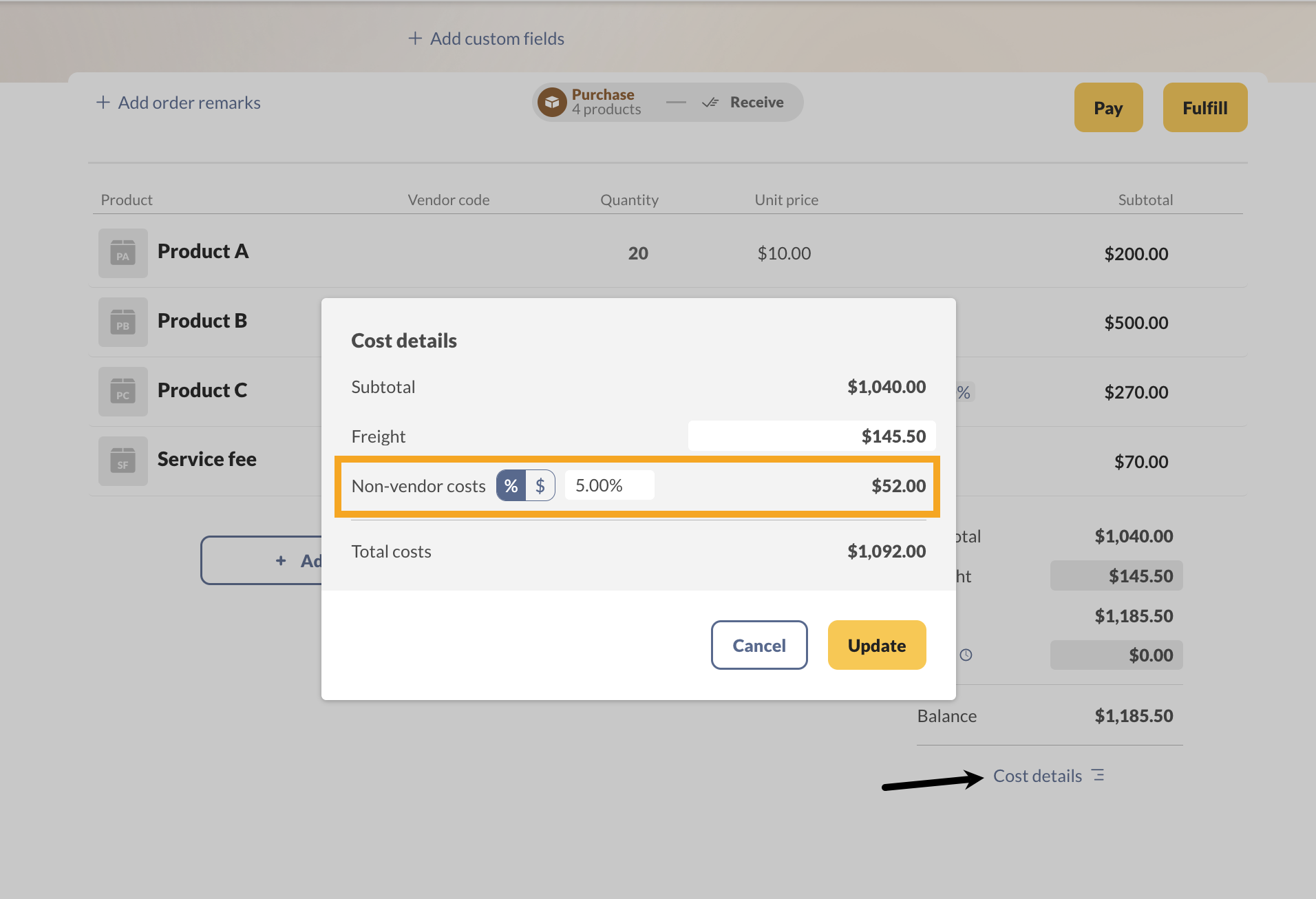
How inFlow calculates non-vendor cost value for each product
Unit Price ÷ Sum of Stocked Products subtotal × Non-vendor Cost% × Order Subtotal = Non-vendor cost per unit
Following the example purchase order above, you would get the following values:
Non-vendor cost (unit)
- Product A: $10 ÷ $970 × (5% × $1040) = $0.53608247
- Product B: $100 ÷ $970 × (5% × $1040) = $5.36082474
- Product C: $27 ÷ $970 × (5% × $1040) = $1.44742268
inFlow for the web shows a maximum of five decimal places, but it performs calculations using the full value in the background.
It is also possible to input a dollar value instead of a percentage for the Non-Vendor Cost. In this case, it would be:
Unit Price ÷ Sum of Stocked Products subtotal × Non-vendor Cost ($) = Non-vendor cost per unit
Service items
If your vendor charges a separate service fee (e.g., polishing, engraving, machining, etc.), inFlow includes the service fee in the cost calculations as well. You would add this service fee to your purchase order as a service-type item.
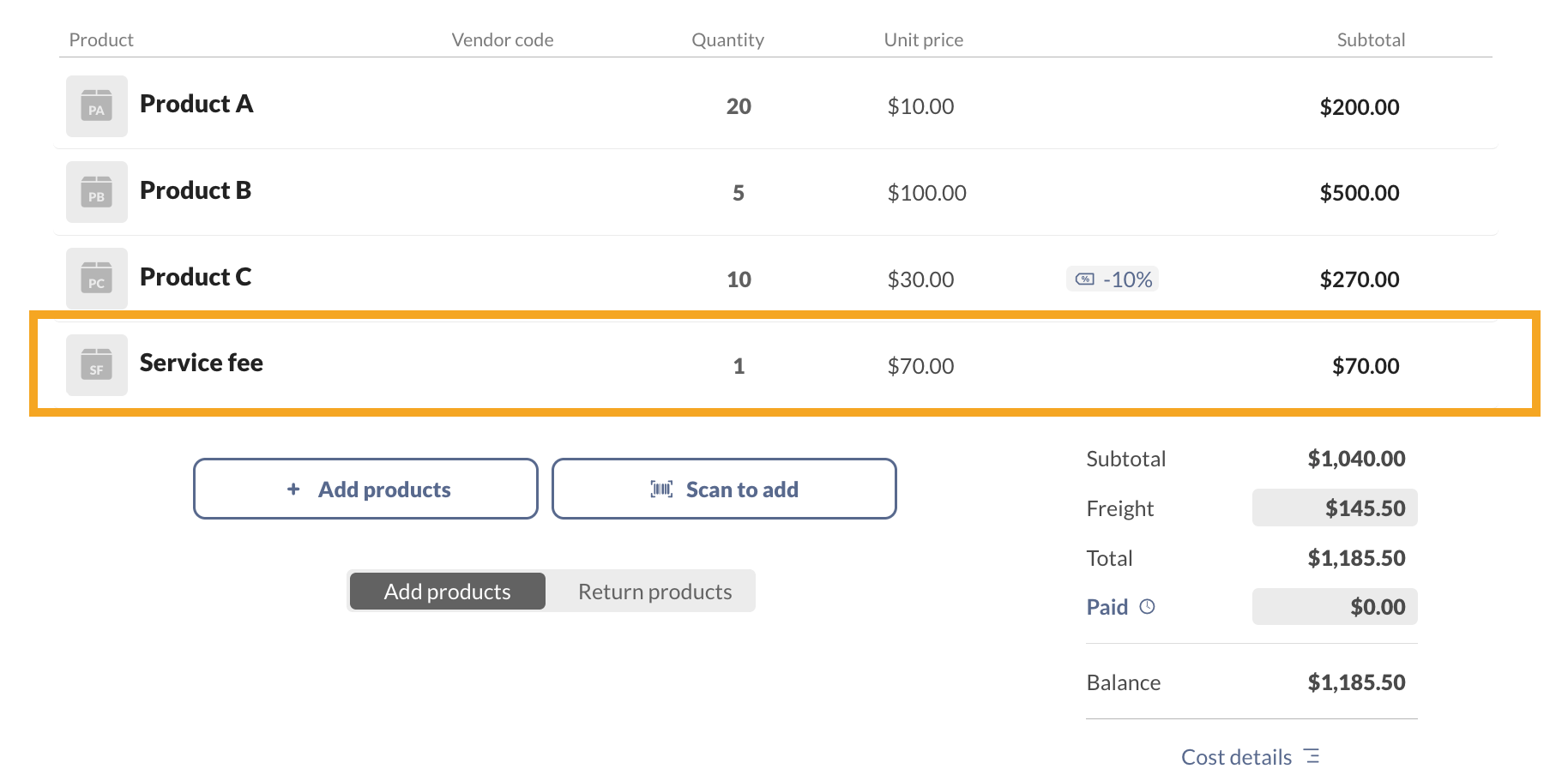
inFlow will include the service fee in the cost of each product. If a service fee only applies to select products, you may want to make two orders so that the service + related items are separate from the other non-serviced items. Service fees are weighted based on the unit price of the products in the order.
For example, if you order a few products from your vendor and one of them needs a polishing service, the polishing fee will be factored into the product costs of all the products on your order, including the ones that don’t need it.
To get the service fee for each product
[Unit Price ÷ Sum of Stocked Products subtotal] × Service Total = Service cost (unit)
Following the example purchase order above, you would get the following values:
Service cost (unit)
Product A: $10 ÷ ($1040 – $70) × $70 = $0.72164948
Product B: $100 ÷ ($1040 – $70) × $70 = $7.21649485
Product C: $27 ÷ ($1040 – $70) × $70 = $1.94845361
inFlow for the web shows a maximum of five decimal places, but it performs calculations using the full value in the background.
Putting it all together… (unit price, non-vendor costs, & service fees)
Phew! That’s a lot of math … It’s a good thing inFlow’s doing all the calculations for you! Adding all the above factors together will give you the cost that inFlow uses for your profit calculations:
Cost of Product A = vendor unit price (including any discounts) + shipping fee/freight + any non-vendor costs + service items on the purchase order.
Cost breakdown for Product A = $10 + $1.50 + $0.53608247 + $0.72164948 = $12.75773195 (inFlow will display $12.75773 in the product record cost field)
- Unit price: $10.00
- Freight: $1.50
- Non-vendor costs: $0.53608247
- Service fees: $0.72164948
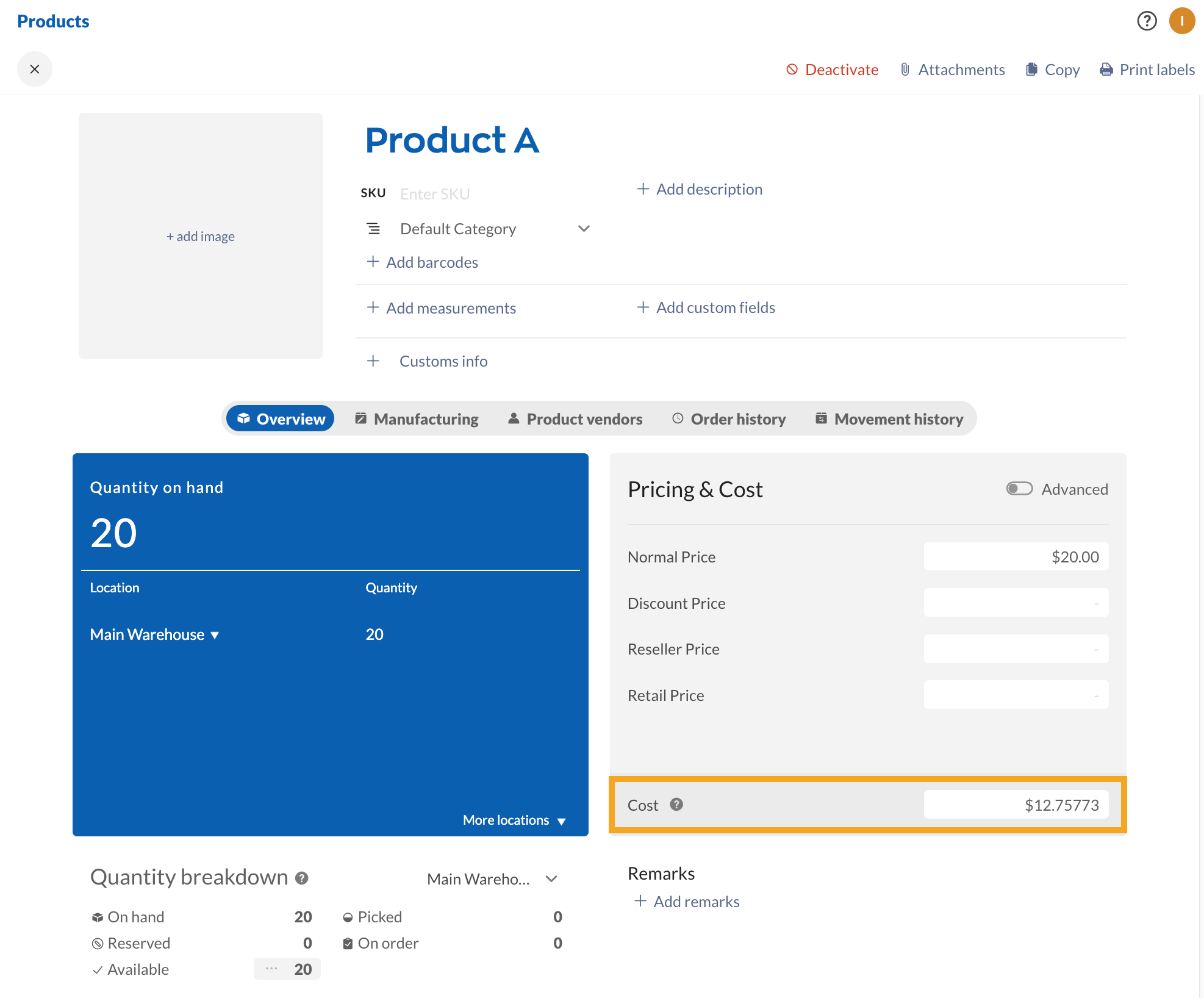
We’ve included a final image here of Product A’s unit cost as calculated by the program from the Product cost report (the cost is rounded up to $12.76).
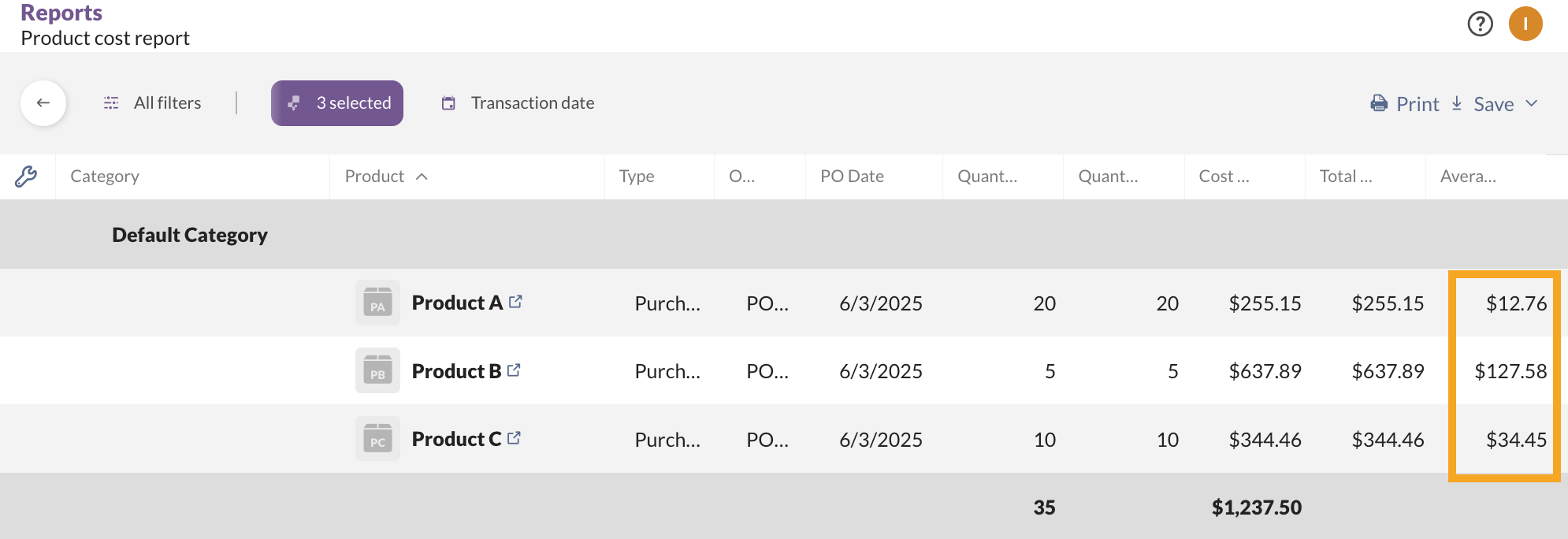
Manufacturing
When manufacturing in inFlow, the product cost is calculated based on the cost of raw materials/components, operational costs, and any additional costs/fees that are tracked in the Other costs field.
Before manufacturing, you can see material and operations cost estimates in the Manufacturing tab on the product record.
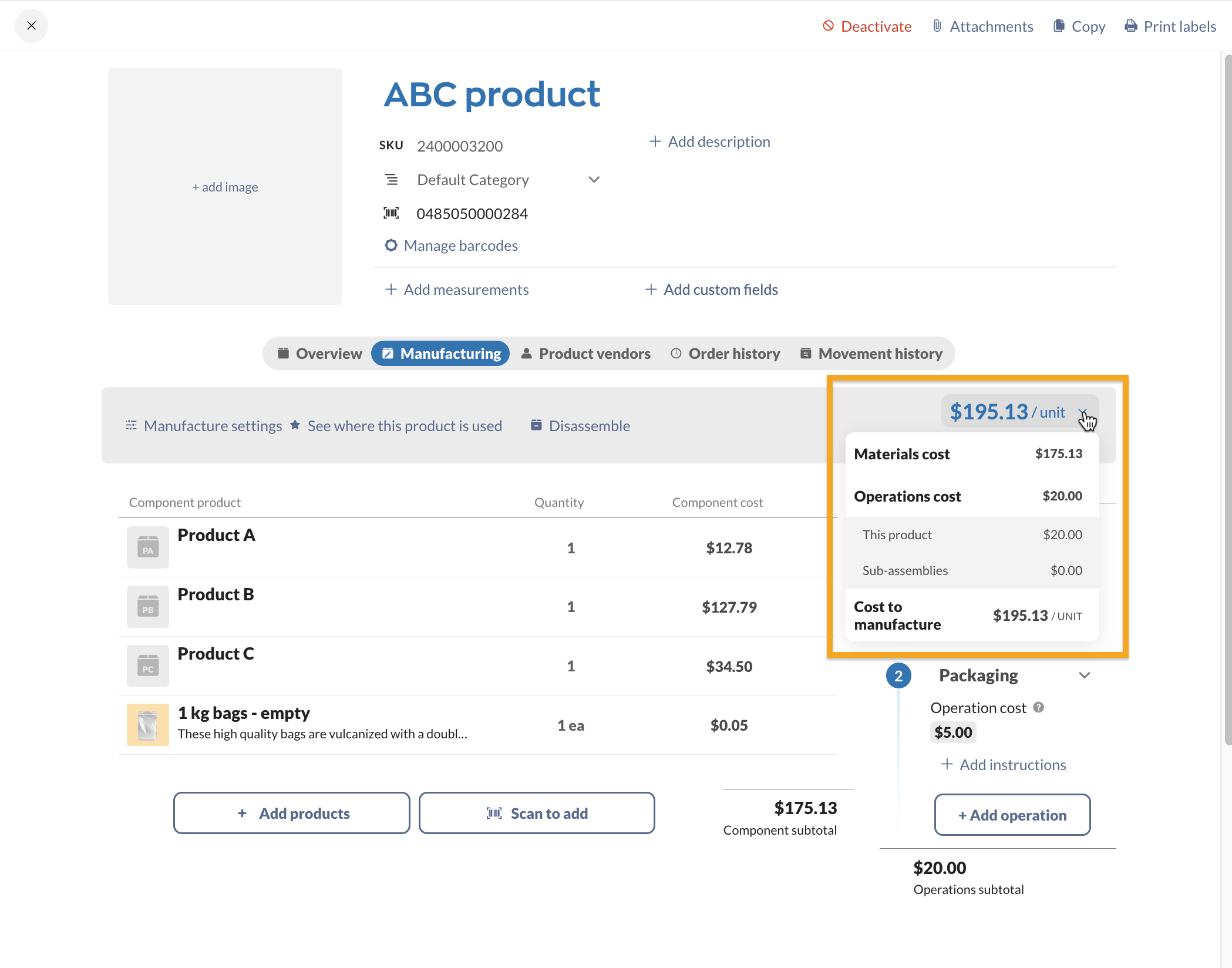
Cost to manufacture breakdown
Cost type | Explanation |
---|---|
Materials cost | The total cost of all of the operations to manufacture one standard unit. This includes any operation costs involved with manufacturing sub-assemblies for one standard unit. Per-unit costs and labor costs are part of the operational costs. |
Operations cost | Sub-assemblies are components that require assembly before you can complete the final product. This amount is for the operations cost of sub-assemblies only. |
Operations cost: This product | This is the cost of directly manufacturing the product. |
Operations cost: Sub-assemblies | Sub-assemblies are components that require assembly before you can complete the final product. This amount is for the operational costs of sub-assemblies only. |
Cost to manufacture vs product cost
Cost to manufacture
This is the estimated cost to manufacture one standard unit (how the product is typically assembled), which is found on the Manufacturing tab of the product record.
Cost to manufacture = material cost + operation costs
Product cost
This is a calculated cost based on the actual purchase/manufacturing and a number of factors across inFlow. This cost is listed on the Overview tab of the product record.
- Vendor unit price (including any discounts)
- Shipping fee/ freight
- Non-vendor costs
- Service items on the purchase order
- Manufacturing expenses (cost of components, operations, and other costs on manufacture orders)
Manufacture order cost example
Let’s take a look at how inFlow calculates the product cost when manufacturing. This example uses the moving average costing method.
Manufacture order: MO-000017
Other costs: $30.00
Finished products:
- ABC Product qty: 1
- ¾” Pump Flange Kit qty: 1
On manufacture orders, you can choose the number of units to create and build multiple finished goods.
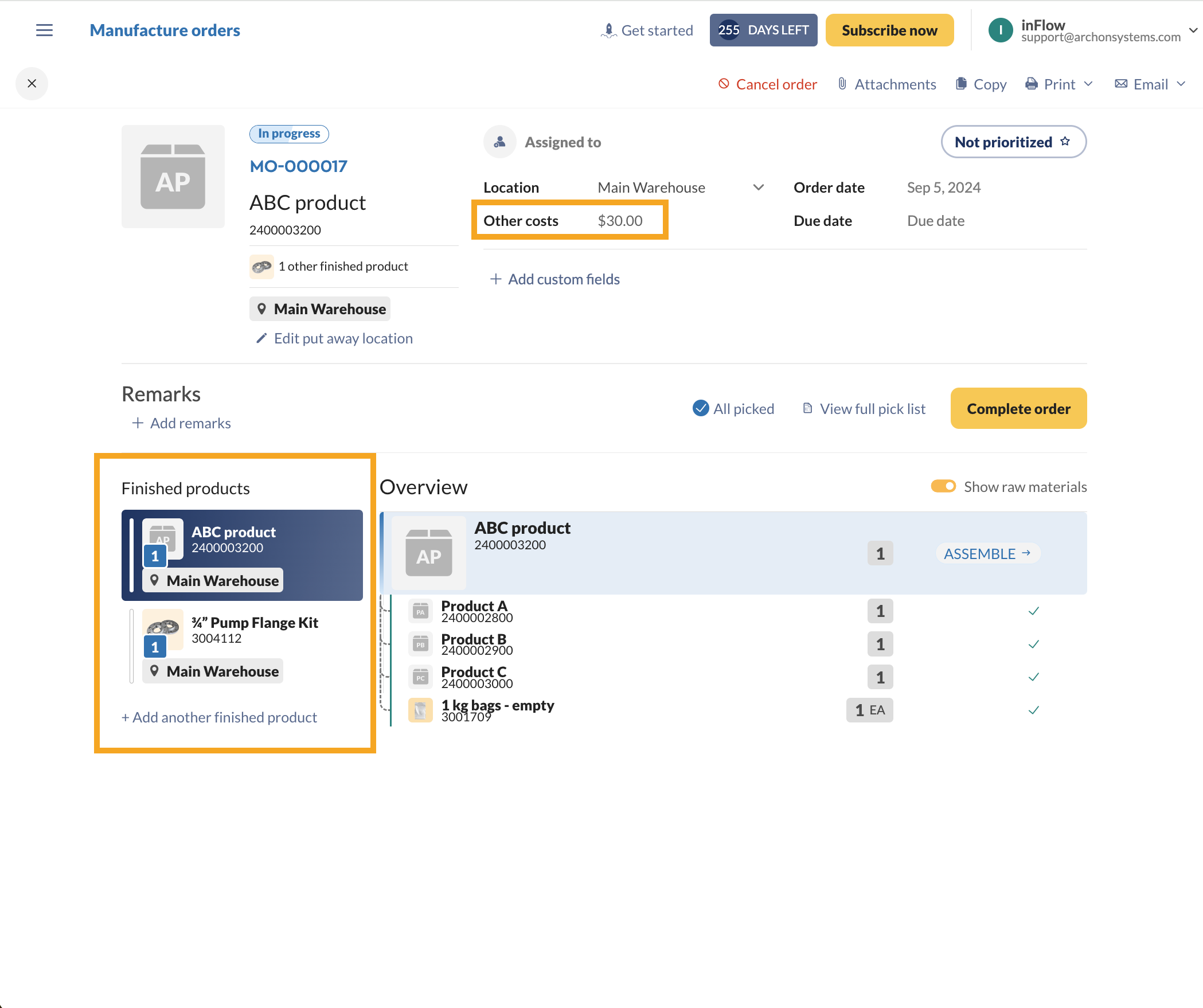
Other costs
The Other costs field is for tracking additional expenses that occur during manufacturing (outside of material and operations costs). inFlow takes the amount in the Other costs field and distributes it across all finished products on the manufacture order. This distribution is weighted based on the component costs of the finished product(s).
Other costs per unit calculation formula
Total cost to manufacture ÷ [Sum of Finished Products cost] x Other Costs Total = Other Costs (unit)
Operation costs
During the Assembly phase, click the pencil icon to make changes to the raw materials and operations as needed.
Updating the hourly labor and duration will allow inFlow to calculate accurate manufacturing costs. Changes/customizations made to manufacture orders are accounted for in the product cost and are divided up by how many units are being manufactured.
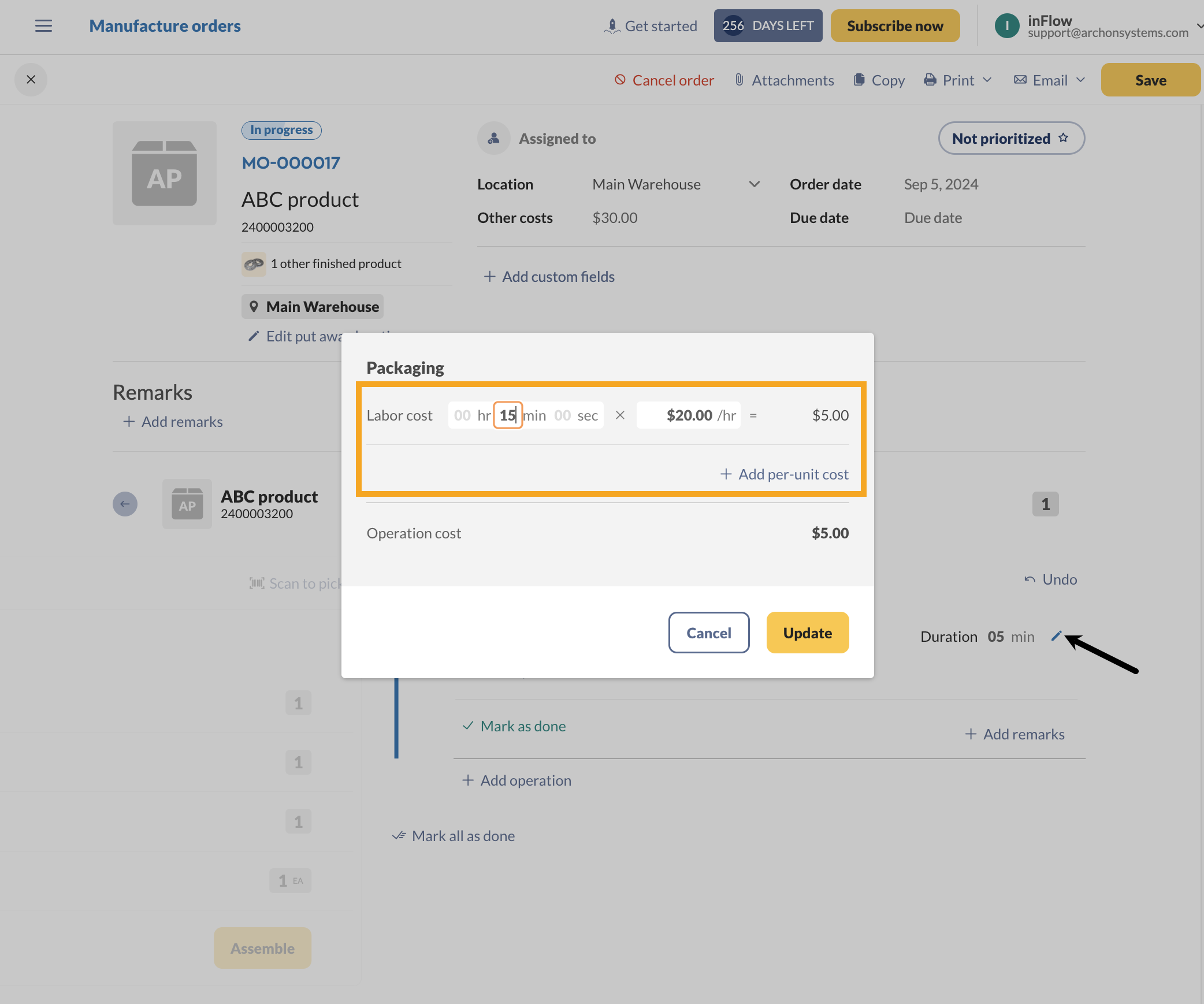
When manufacturing is complete, the updated costs can be found in the Product cost report.
ABC product – $223.72
- Cost to manufacture a standard: $195.13
- Other costs from MO-000017: $28.59
¾” Pump Flange Kit – $10.99
- Cost to manufacture: $9.58
- Other costs from MO-000017: $1.41
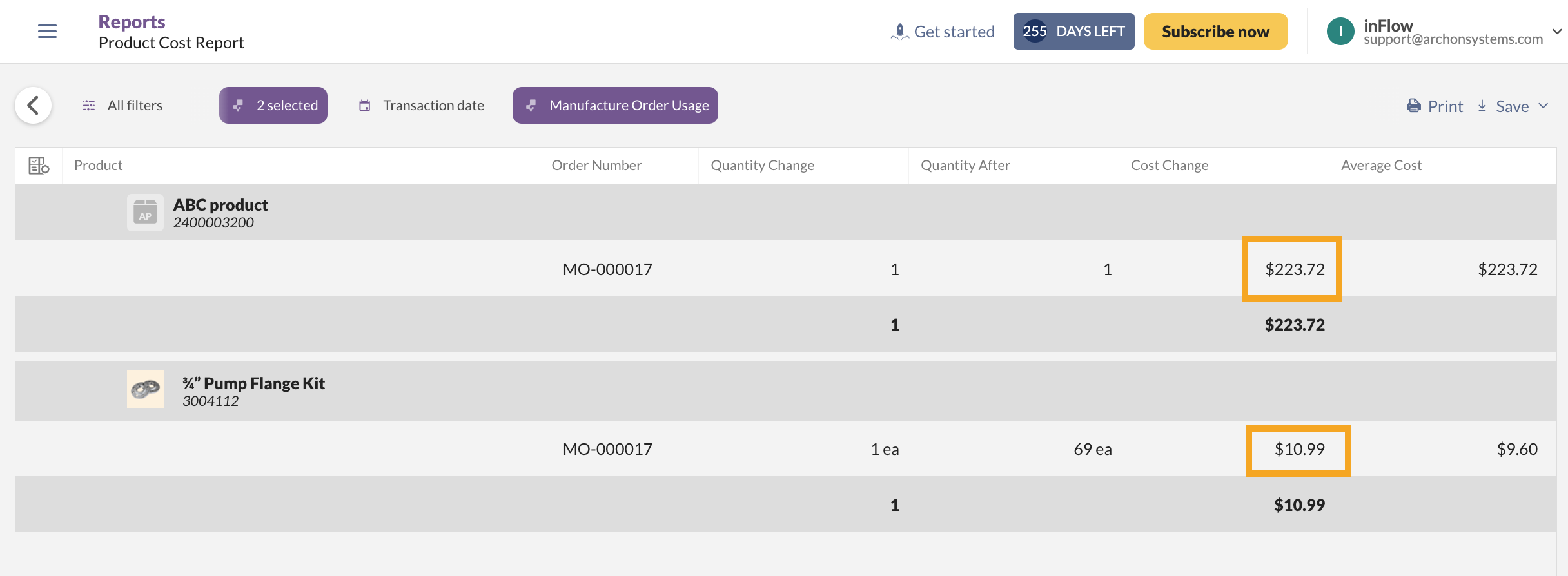
Windows
inFlow calculates the cost of a product as it enters your inventory (via purchase or manufacture orders) based on several factors:
- Vendor unit price (including any discounts)
- Shipping fee/ freight
- Non-vendor costs
- Service items on the purchase order
- Manufacturing (operations, cost of components, and other costs on manufacture orders)
inFlow does not include any taxes on the purchase order when calculating the cost.
We’ll use a sample purchase order to help illustrate the above factors in detail.
Vendor Unit Price
The purchase order displays the vendor unit price in the Unit Price column. If a product has a discount, it affects the Subtotal column on the order.
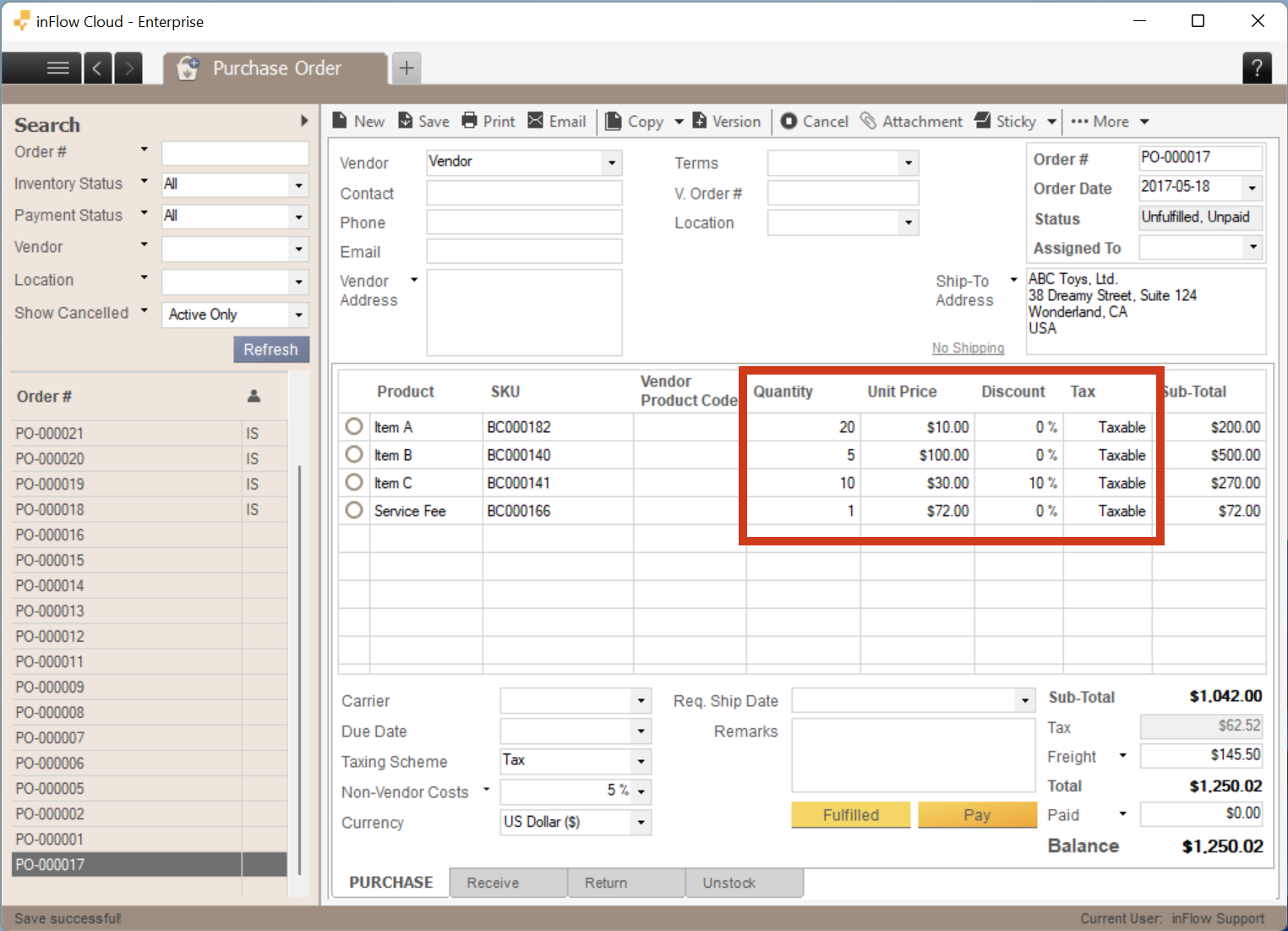
To get the unit price for each product
Product Subtotal ÷ Product Quantity = Unit Price
Following the example purchase order above, you would get the following values:
Vendor Unit Price (incl. discount)
Product A: $200 ÷ 20 = $10
Product B: $500 ÷ 5 = $100
Product C: $270 ÷ 10 = $27
Freight
If your vendor is charging you freight/shipping fees, you can input that in the Freight field (above the order total).
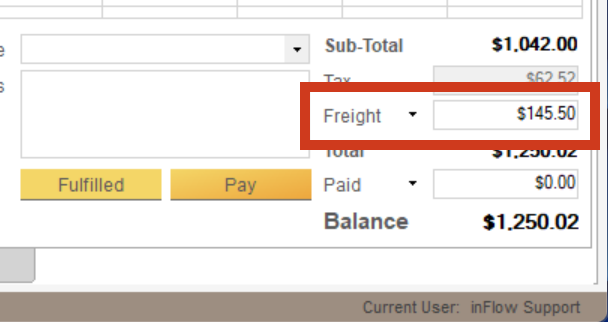
If you don’t see this field in your purchase order, you’ll need to click the Add Shipping button at the top right to enable shipping.
This example order has tax on shipping/freight enabled.
inFlow takes the amount in the Freight field and distributes it across all stocked products on the purchase order. This distribution is weighted, and it depends on the unit price of the product.
To get the freight value for each product
Unit Price ÷ [Sum of Stocked Products subtotal] × Freight Total = Freight (unit)
Following the example purchase order above, you would get the following values:
Freight (unit)
Product A: $10 ÷ [ $970 ] × $145.50 = $1.50
Product B: $100 ÷ [ $970 ] × $145.50 = $15
Product C: $27 ÷ [ $970 ] × $145.50 = $4.05
Non-vendor costs
If you need to pay any duties/ import fees/tariffs, you’ll need to record this under the Non-Vendor Cost field (bottom left of the purchase order). These charges should be added only if the payment isn’t going to your vendor. Any extra fees that require you to pay your vendor should go in either the freight field or as a service fee on the order itself, not non-vendor costs.
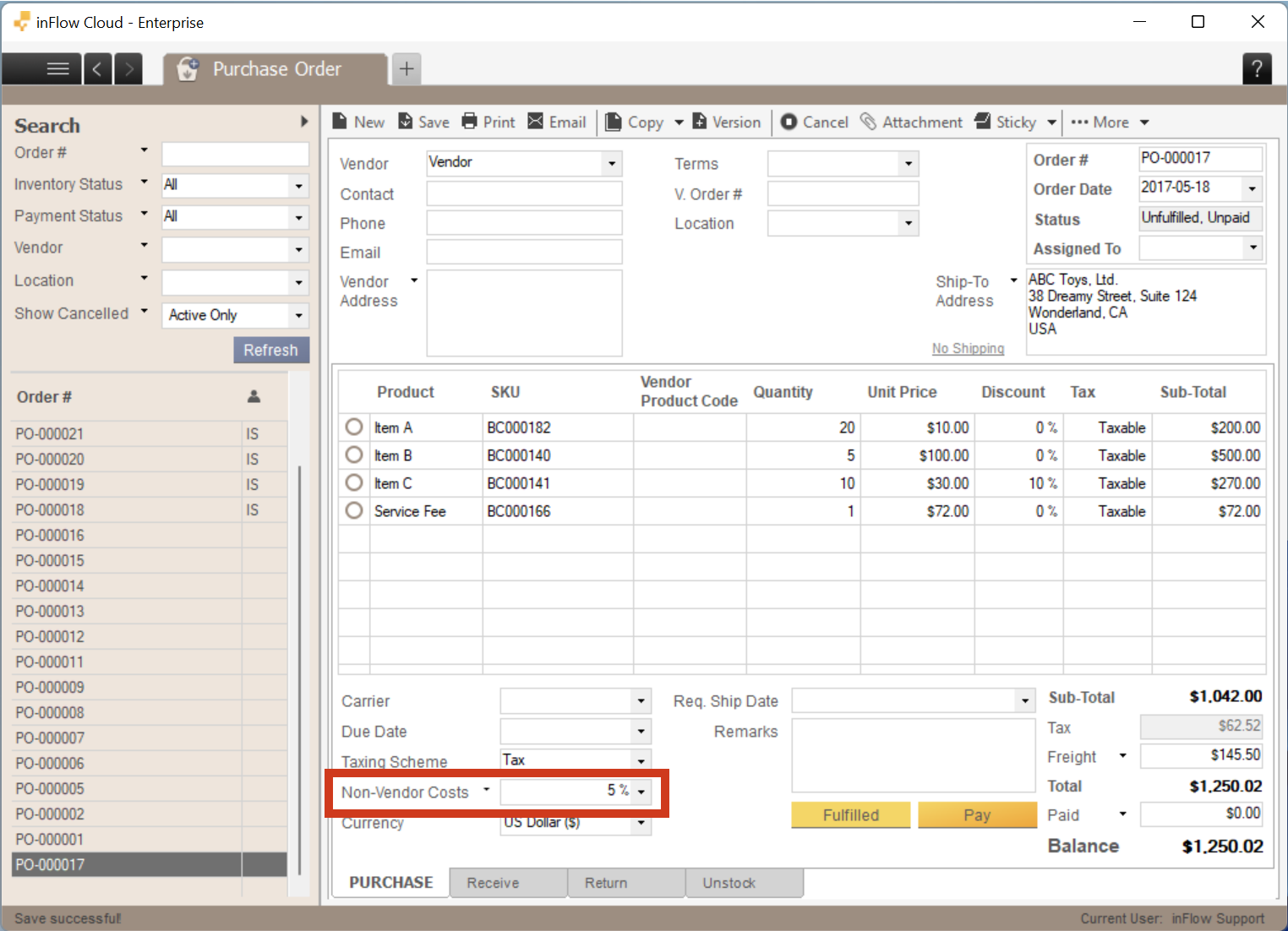
To get the non-vendor cost value for each product
Unit Price ÷ [Sum of Stocked Products subtotal × [Non-vendor Cost % × Order Subtotal] = Non-vendor cost (unit)
Following the example purchase order above, you would get the following values:
Non-vendor cost (unit)
Product A: $10 ÷ [ $970 ] × [ 5% × $1042 ] = $0.53711
Product B: $100 ÷ [ $970 ] × [ 5% × $1042 ] = $5.37113
Product C: $27 ÷ [ $970 ] × [ 5% × $1042 ] = $1.4502
It is also possible to input a dollar value instead of a percentage for the Non-Vendor Cost. In this case, it would be:
Unit Price ÷ [Sum of Stocked Products subtotal] × [Non-vendor Cost ($)] = Non-vendor cost (unit)
Service items
If your vendor charges a separate service fee (e.g., polishing, engraving, machining, etc.), inFlow includes the service fee in the cost calculations as well. You would add this service fee to your purchase order as a service-type item.
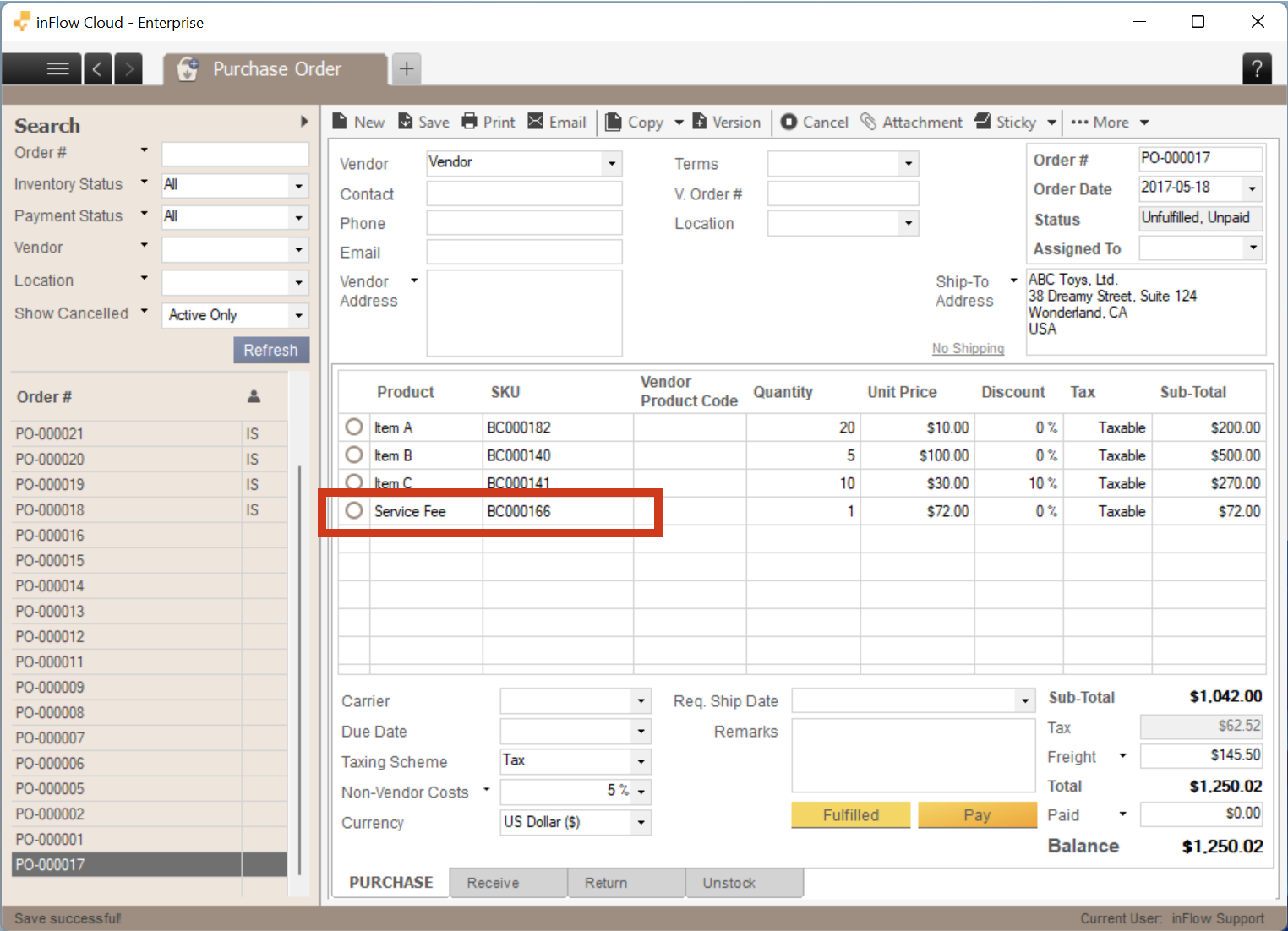
inFlow will add the service fee to each product’s cost. You may want to place service and related items in one order and keep non-serviced items in a separate order.
Let’s say you bought some products from your vendor, but only one item has an extra fee for polishing. When you add more items to the same order, the polishing service fee applies to each product, even if some are not serviced.
To get the service fee for each product
[Unit Price ÷ Sum of Stocked Products subtotal] × Service Total = Service cost (unit)
Following the example purchase order above, you would get the following values:
Service cost (unit)
Product A: $10 ÷ [$1042 – $72] × $72 = $0.74227
Product B: $100 ÷ [$1042 – $72] ×$72 = $7.42268
Product C: $27 ÷ [$1042 – $72] × $72 = $2.00412
Putting it all together…
Phew! That’s a lot of math … It’s a good thing inFlow’s doing all the calculations for you! Adding all the above factors together will give you the cost that inFlow uses for your profit calculations:
Cost of Product A = vendor unit price (including any discounts) + shipping fee/ freight + any non-vendor costs + service items on the purchase order
Cost of Product A = $10 + $1.50 + $0.53711 + $0.74227 = $12.77938
We’ve included a final image here of Product A’s unit cost as calculated by the program:
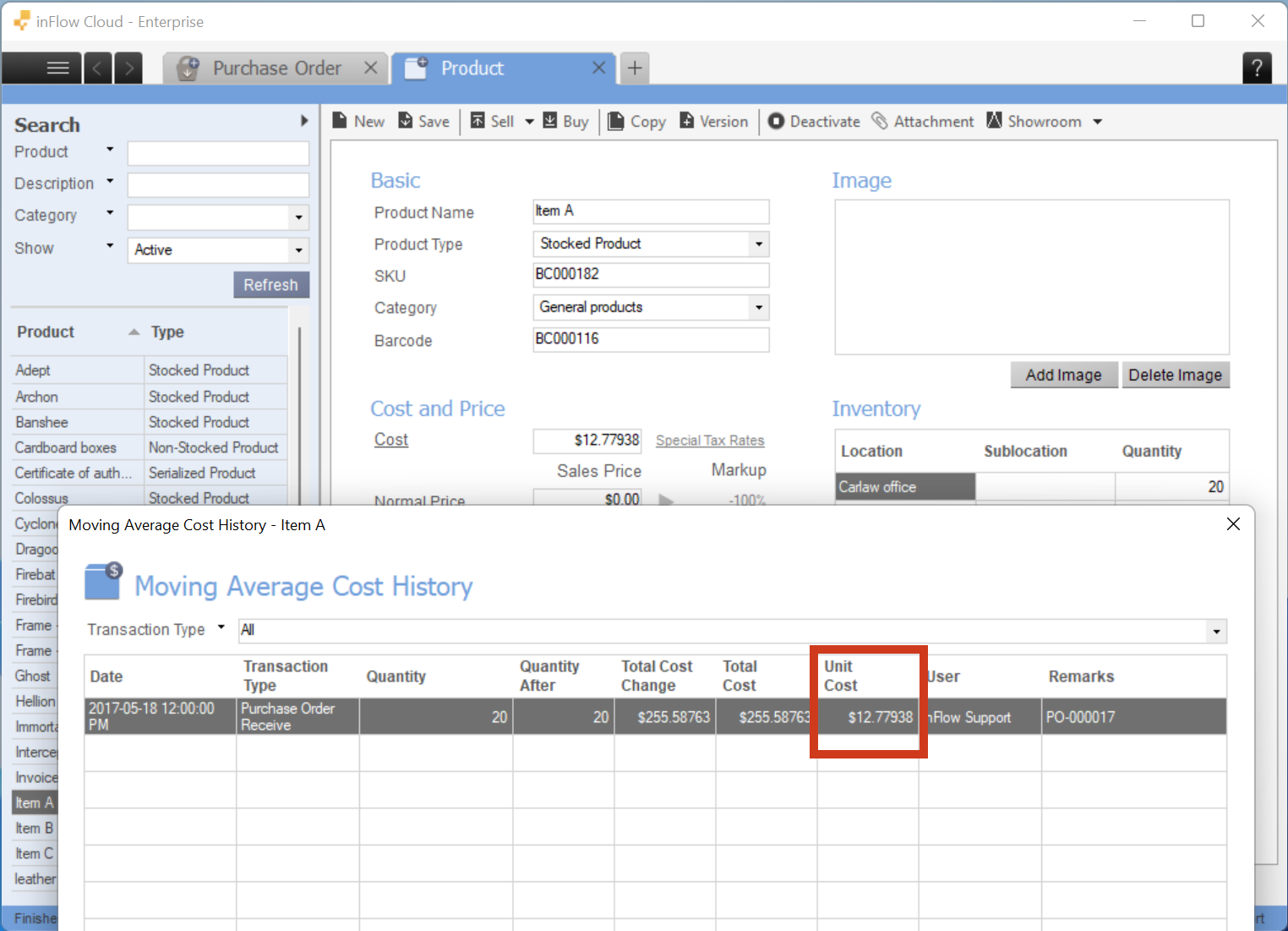
0 Comments