Every fresh piece of produce or beautifully baked loaf of bread has a limited lifespan. When food starts to go bad, you must pull it from the shelves and throw it away. It is no longer considered safe for human consumption. Unfortunately, Americans waste nearly 40 percent of all food. This accounts for $408 billion of food — 130 billion meals — thrown out annually. While a single business can’t solve this crisis, good shelf life management can help a company reduce its levels of waste.
While waste occurs throughout the food chain, retailers could significantly reduce the amount of food thrown out. This is good for the planet and can also improve business performance. Look at your current inventory system and consider how you can improve it. You might be able to cut back on waste with a few minor updates to your operations.
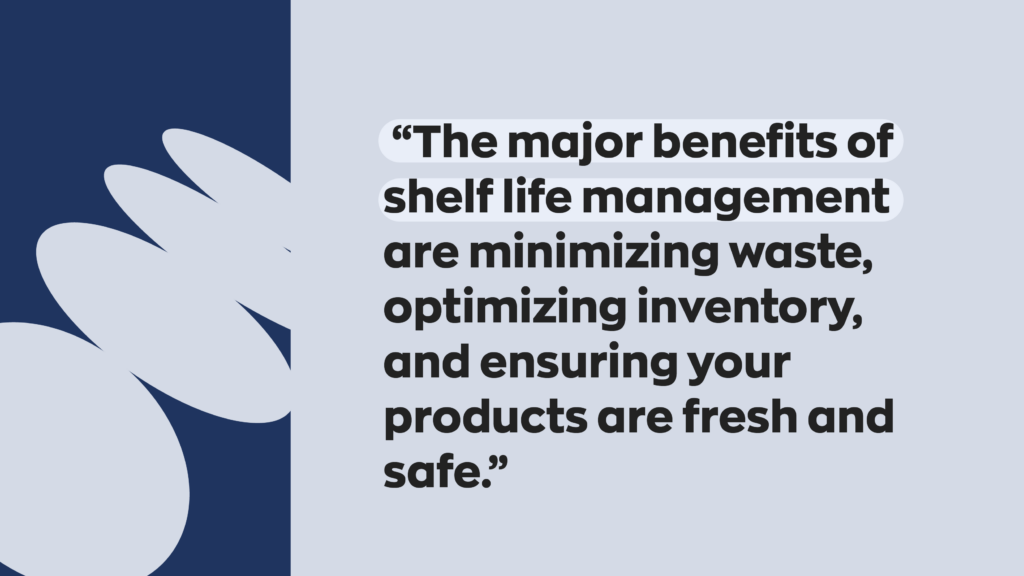
Consider automated inventory controls
The first step toward reducing food waste is to set up automated controls throughout your organization. Not only will automated systems reduce human error, but they can also streamline your operations. These tools can make adjustments and handle your inventory with more care than an entire team of employees. Here are a few opportunities to explore:
- Temperature or humidity controls protect your delicate products and maintain stable temperatures throughout the day. Some systems can also adjust humidity levels based on what you are trying to store.
- Quality testing ensures your food meets the U.S. Food and Drug Administration’s standards for safety. This reduces waste by identifying contamination before it spreads.
- Automatic pull systems minimize waste through lean manufacturing, which only pulls the specific products you need. This is more efficient than ordering the same amount each time. You can also use manufacturing software to streamline ingredient sourcing and storage.
- Minimal stock alerts lower your minimal stock level, and use automated alerts to know when you need to replenish your stored food.
There is no single solution for cutting back on food waste. Instead, you can implement multiple new systems that all contribute to preserving the food you have on-site.
Use QR codes for data-rich labeling
One of the most powerful tools in inventory management is data-rich labeling, either through QR codes or barcodes. A barcode stores data about a product and reports this information when scanned. A QR code is a more advanced form of the bar code. It can hold significantly more information, which is valuable for brands.
By investing in a QR code system, you can catalog more information about your food and other items. This makes management easier and allows you to track products on a micro level.
Actualize first-in, first-out logic
First-in, first-out (FIFO) logic is essential for moving perishable items. It is the idea that your oldest inventory — the first products you added to your business — should be moved before the newest. This is why many grocery stores have systems in place when they stock perishable products like milk from the back of the store. It pushes the oldest milk to the front so it gets sold. Otherwise, the oldest milk would be stuck in the back forever until it spoiled.
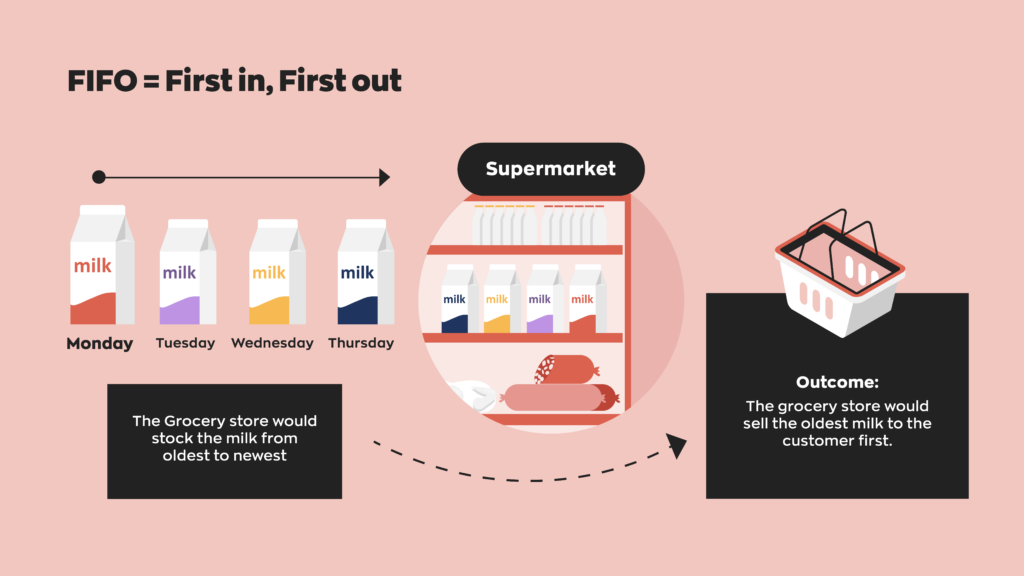
This is one of the first systems you can implement with your data-rich barcoding system. You can assign dates to your inventory to know when they were produced or arrived in your facility. This empowers you to select the first-in products each time to prevent waste.
Use an inventory management system
You don’t need to be an expert in operations management to reduce your food waste. Instead, you can invest in a software system to do that for you. Inventory control software, like inFlow, provides clarity into which materials are coming into your business and which products are going out. We designed our software to track SKUs for you and allow you to make adjustments for increased optimization.
Our software can also help with other aspects of product management. For example, it can keep up with your FIFO best practices so you always move the first-in inventory first. You can also further prevent waste by following buyer trends. inFlow can highlight which products are the least desirable so you can reduce your inventory and focus on higher-demand items.
Do smart demand forecasting
Forecasting examines past trends to make future predictions. Accurate forecasting uses a mixture of short-term data and long-term trends to identify potential customer needs. For example, year-over-year data can prove that people eat more ice cream during summer. However, quarterly or monthly data can show that raspberry is currently one of the most in-demand flavors. This information would tell an ice cream retailer to increase their inventory, focusing on raspberry options.
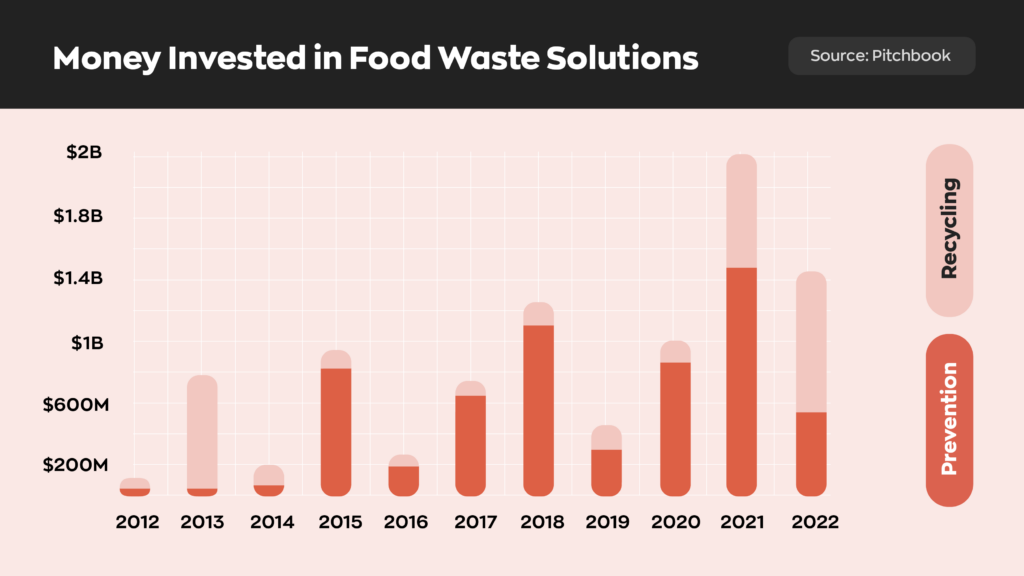
Inventory forecasting reduces waste by predicting increases and decreases in demand. While it isn’t perfect, it can help teams make strategic decisions by looking at various trends. As your inventory software collects more data points — especially through barcoding — your system can get better analytics information, resulting in smarter forecasting.
Optimize collaboration with suppliers
Another way to optimize shelf life is to work with wholesale suppliers. These companies work with customers of all sizes and can accommodate your inventory needs. As your management systems become more advanced, you can adjust your orders with your vendors to prevent waste. These suppliers can also use wholesale inventory software to optimize distribution on their end.
There is also a place for warehouse management software in your supply chain as well. These tools can optimize storage to maximize shelf life and staffing to ensure products move effectively. All areas of your business operations can benefit from greater insight and management processes.
Improve staff training and implementation
Good tools can help companies reduce waste but require employees to buy into them. When your employees are knowledgeable and eager to use the tools, they can get the most out of them. Your team can also look for new ways to preserve your inventory and maximize its shelf life.
Make waste reduction part of your company’s core values. Highlight both the financial cost to your company of wasted food and the environmental impact of lost inventory. Train and retrain your staff as needed. This way, everyone in your company is focused on good inventory management.
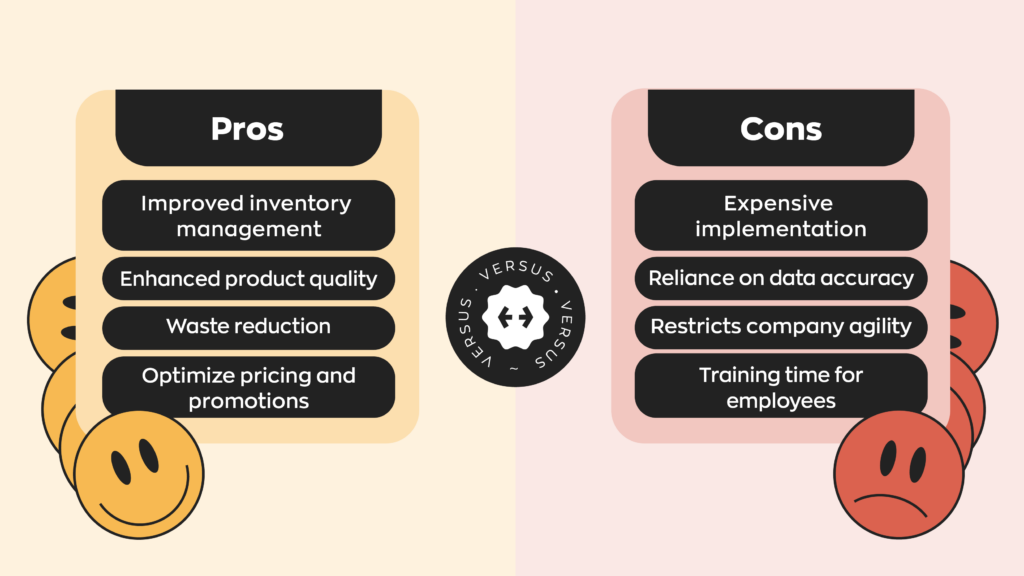
Pursuing continuous improvement
Many of these processes you implement in your organization aren’t one-time improvements. Instead, you will likely continuously work to extend the shelf life of your inventory and optimize your operations. Here are a few ways that you can keep tracking your inventory while looking for new ways to reduce waste:
- Conduct regular audits: Frequently check your inventory and waste levels to see if anything has changed. Identify shifts in your inventory and determine how to address them.
- Communicate with suppliers: Make sure your suppliers understand your goals and are equally committed to reducing waste. Develop agreements with them that align with your agility goals and lean methods.
- Encourage employee feedback: The best ideas come from the people working within your organization. Make it possible for your employees to share insights and suggestions for improving the management of your products.
Most importantly, make sure you have a management software system that you can trust. The right tools will help you find new ways to improve your operations and reach your waste reduction goals.
0 Comments