For years, studies have shown that the workplace environment has a direct correlation with productivity levels. The less stressful the workplace, the more satisfied and productive your employees will be. Today, healthy, efficient, and positive work environments that are less cluttered and more organized are considered highly conducive to increased performance levels.
Around 87% of workers prefer to work at a company that offers a healthier work environment. Of course, this includes an offering of health and wellness benefits and amenities. It also means an overall workspace that is clean, healthy, organized, and efficient. All things that can be provided through better space management strategies.
Furthermore, space management can also help a company be more sustainable by cutting down on clutter and excess of inventory. Often, sustainability and space efficiency go hand in hand. Using tools like warehouse management software will help you buy and use less stuff. Additionally, it will help with automation and optimization which means you’ll create less waste and consume less energy.
Overall, the many benefits of space management include:
- Improved space utilization (no wasted space)
- More cost-efficient
- Better collaboration and productivity
- Improved workflow and traffic flow
- Better energy efficiency
- Reduced waste
- Overall improved facility management
- Improved planning for company growth
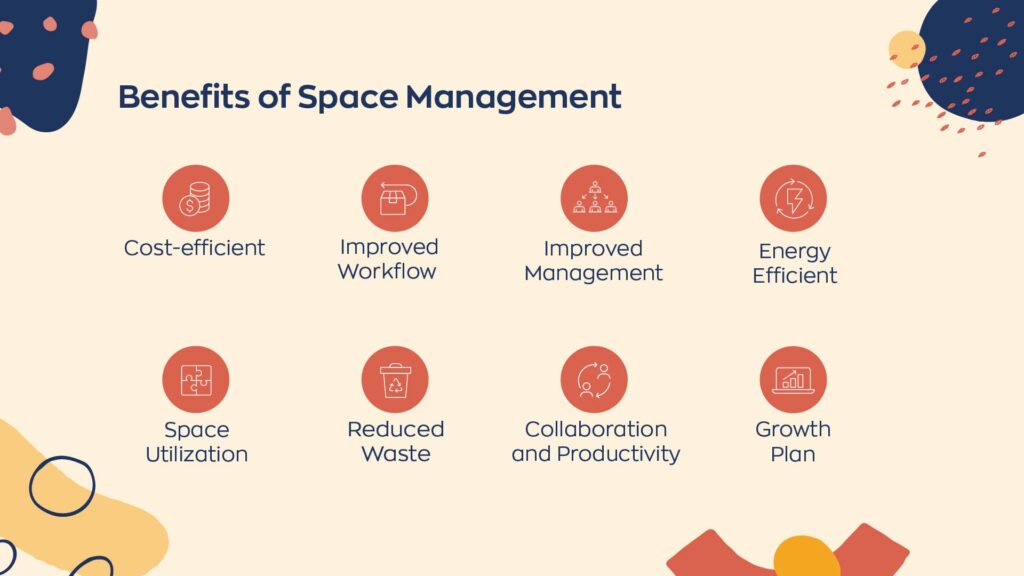
With space management, you can create workspaces that are more organized and efficient. Whether it’s a warehouse, storage areas, an office, or customer-facing stores, you’ll be better able to handle growth and an influx of new employees and more inventory.
Assess current data
The first step to space management is gathering useful data on your workspace and workforce. You can use this data to identify pain points and issues that need addressing before making any changes.
Floor plans and square footage
First, you will need data on your entire facility space, including the layout and the square footage. This will give you a better understanding of how overall flow and utilization are affected by your layout. You can access this information using AutoCAD. Not everyone will have access to AutoCAD floor plans or someone that can create them for you. In this case the building architect or building manager should be able to provide you with the info you need.
Workplace efficiency
Next, you’ll want to look at how efficient everything is working in regards to your organization’s structure. Including the flow of inbound and outbound products. This data can be accessed through your finance systems, such as Workday Financial Management or SAP.
Employee satisfaction
The final step in the data analysis process is to review personnel data to get an idea of overall occupancy, employee satisfaction, and productivity levels. You need to know how many people are working in the space. Ask them what issues they may be having, and how productive they are. This will give you a good sense of what areas need improvement to create a more efficient workspace.
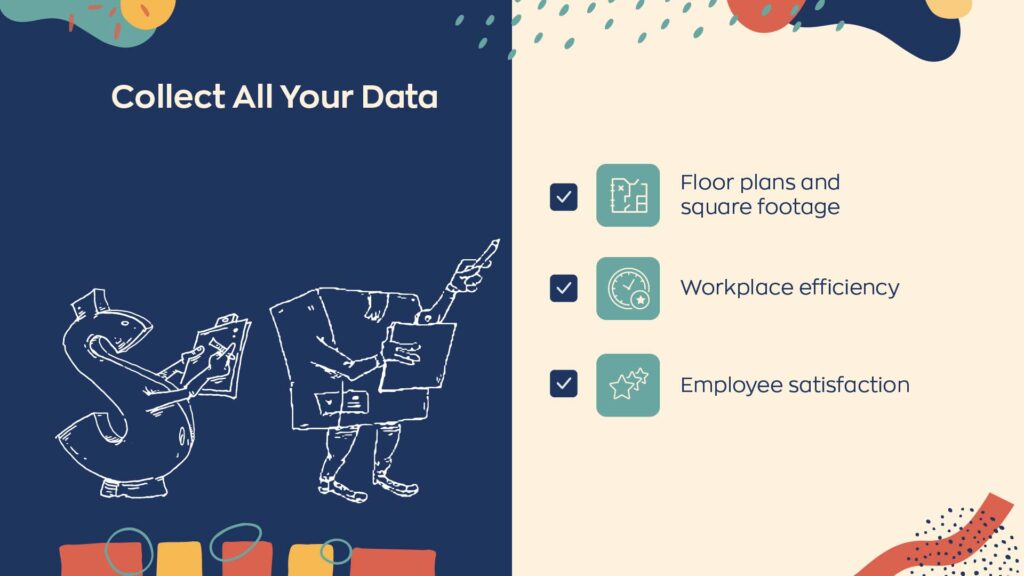
Go vertical
After you’ve analyzed all the data, it’s helpful to walk through your physical workspaces to get an idea of how your vertical space is being used and how your inventory could be redistributed and reorganized. Some businesses only pay attention to what is at eye level or below it. But your vertical space is just as useful for storing and reorganizing inventory. Going vertical can help you better utilize the square footage available. Make sure not to violate any health and safety regulations.
Identify duplicate systems
In many cases, when a company has too much inventory, and their space is disorganized, they often find that they have duplicate storage systems or multiple locations or areas where they are storing the same items. This often leads to overstock or inaccurate stock calculations.
You can use various racking systems to combine everything into one convenient area, such as double-depth racking. Additionally, it is essential to start using clear labels and images, such as posters, to help employees better identify where things go. This will help you avoid things once again being duplicated or stored in multiple different areas.
Consolidate overstock
If you are carrying excess inventory after identifying duplicate systems, you can handle the situation in a few different ways. While it can be good to have some safety stock on hand in case customer demand increases, too much overstock can negatively impact business and space management. So it’s important to thoroughly sort through everything to identify what truly needs to be kept and what you can get rid of.
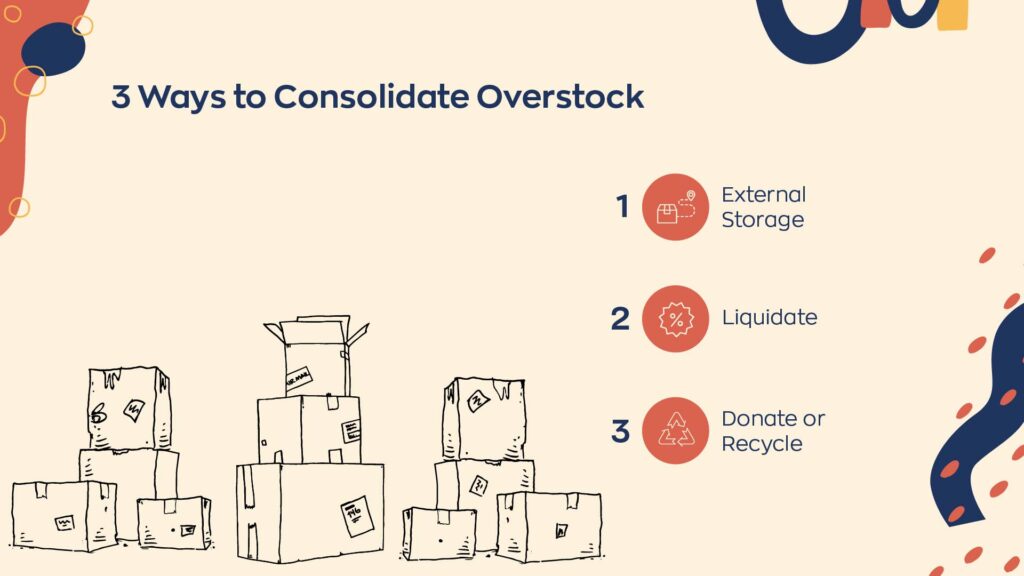
Donate or recycle
If you have too much overstock, consider donating it or recycling it instead of tossing it out. Companies are one of the biggest contributors to waste. This is often because they use too many resources and often dump their waste instead of recycling it. Plastic waste from products and packaging is a particularly significant issue that is damaging the environment. So when you are sorting through your overstock, make sure you find more sustainable ways to get rid of the things you no longer need or find other uses for them.
Liquidate
Another way to get rid of overstock is to find ways to sell it off. If you have too much of a certain item, liquidation is always an option if you need to make room for other products. This can easily be done by dropping the price to entice customers to buy more of it, selling it off at pop-up shops, putting it into bundles for giveaways, or upping your marketing efforts to expand your reach and get more people to buy.
External storage
If you feel it is wasteful to get rid of the excess inventory and think it will be useful to still have on hand, you can look into external storage options. Remember, the goal is to clear out your workspaces to make them more efficient, so if you keep a bunch of overstock in your primary work areas, it will negate the point of space management. If you find you have a lot of overstock due to rapid growth, this could be a good time to start considering expanding and looking into bigger spaces or buying a second warehouse.
Improve traffic flow
Another key element of space management is traffic flow. Good traffic flow, especially in warehouse spaces, is not only good for workflow efficiency, but it’s also important to ensure a healthy and safe work environment for your employees. There are many ways to improve traffic flow in the workspace, including:
- Opting for a street-style open layout, or other types of open layout plans
- Regulating traffic flow by utilizing the same door for shipping and receiving
- Using separation structures, barriers, and barricades to separate and direct the flow of traffic
- Placing floor markings to identify zones and create separate paths for employees and vehicles
- Using signage to mark zones direct which way to go
- Creating safe crossing paths where the flow of traffic intersects
- Clearly labeling and identifying entry and exit points
Optimize with warehouse management software
Utilizing the latest tools and systems is the best way to manage and optimize your workspaces. You shouldn’t be using Excel to keep your inventory because this represents a legacy solution that isn’t as efficient as the new systems that are available today. It is essential for companies to automate as much as they can to improve workflow and productivity, achieve sustainability, and better manage their warehouses and other spaces overall.
A quality warehouse management software solution can help you better optimize your space for efficiency and keep track of numerous aspects of your business, such as asset tracking, inventory control, sales and invoicing, reporting, purchasing and receiving, and more.
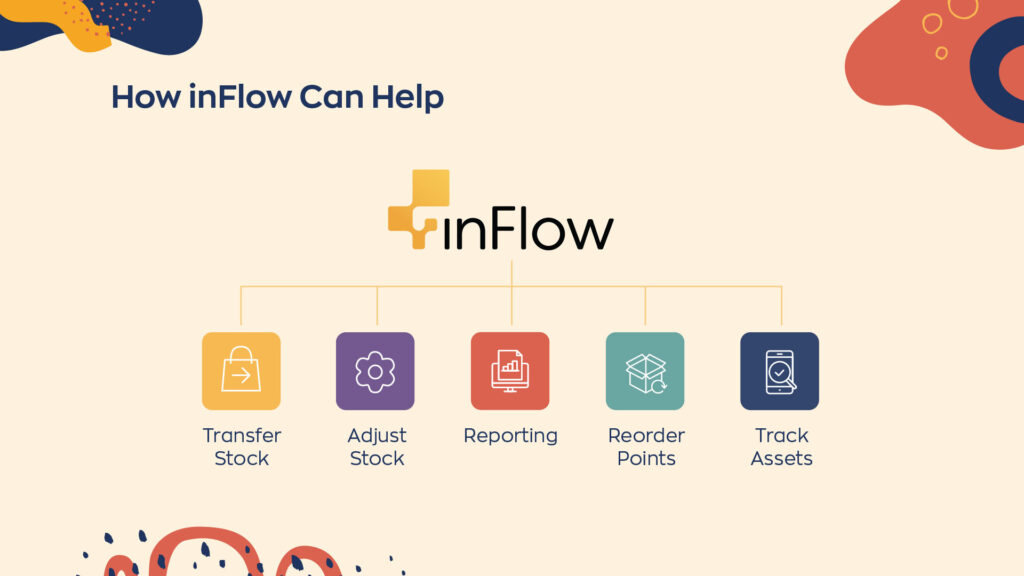
Relocate if necessary
There are several ways business owners can implement changes to maximize and optimize space for efficiency and improved productivity. It’s beneficial to seek out all of your options to find the best solution that works for you and your business. And again, if you have exhausted all other options and are finding it difficult to push forward, it may be time to expand into another space or even relocate to a new area. If this is the route you choose, signing up for a new and better inventory management software solution can help ensure everything stays organized and the process goes as smoothly as possible.
0 Comments