We recently discussed the Toyota Production System (TPS), a core philosophy of lean manufacturing. Another essential part of lean manufacturing is one-piece flow manufacturing. So: what is one-piece flow? How does it relate to other manufacturing methods? What are the benefits of one-piece flow? And, most importantly, when should you be using it?
What is one-piece flow manufacturing?
As the name suggests, one-piece flow (also known as single-piece flow) is a manufacturing process focusing on producing a product one unit at a time. This may sound simple, but there is some nuance to this process.
It’s important to note that in single-piece flow, only one unit is on the assembly line at any time. This means that the production of a new unit doesn’t start until the previous one is complete. This narrow focus means most businesses won’t start production until they receive an order.
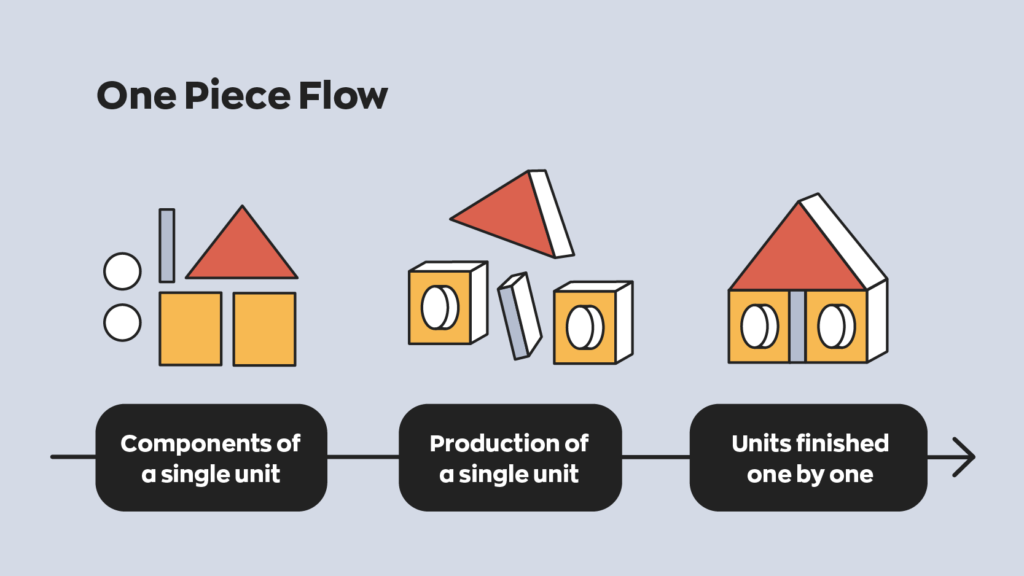
For example, let’s pretend that you own a custom wedding cake business. Because of the nature of your product, there’s no point in making anything until an order comes in. In addition, once you begin working on one order, you’ll probably finish it before starting work on another.
Another important aspect of one-piece flow is minimal inventory. Because there’s only ever one unit in production, there’s no point in stocking up on components. Instead, businesses using one-piece flow keep just enough to produce a single unit and replace components as they use them.
How does this differ from other manufacturing processes?
If you’re looking into one-piece flow, there’s a good chance you’ve stumbled across some similar terms, such as continuous flow or flow production. While they’re similar, some key differences set them apart.
- Flow production (also known as mass production) involves the use of production lines to manufacture many products at once.
- Continuous flow production is similar to flow production. This method of production aims to increase efficiency by minimizing downtime. This means that the production lines are almost always active.
- Batch manufacturing is the most similar to single-piece flow. What sets it apart is instead of manufacturing one unit at a time, batch manufacturing produces multiple units in, you guessed it, batches. After each batch, there is a pause in production. This allows workers to either switch to the production of a different product or wait until another batch is needed.
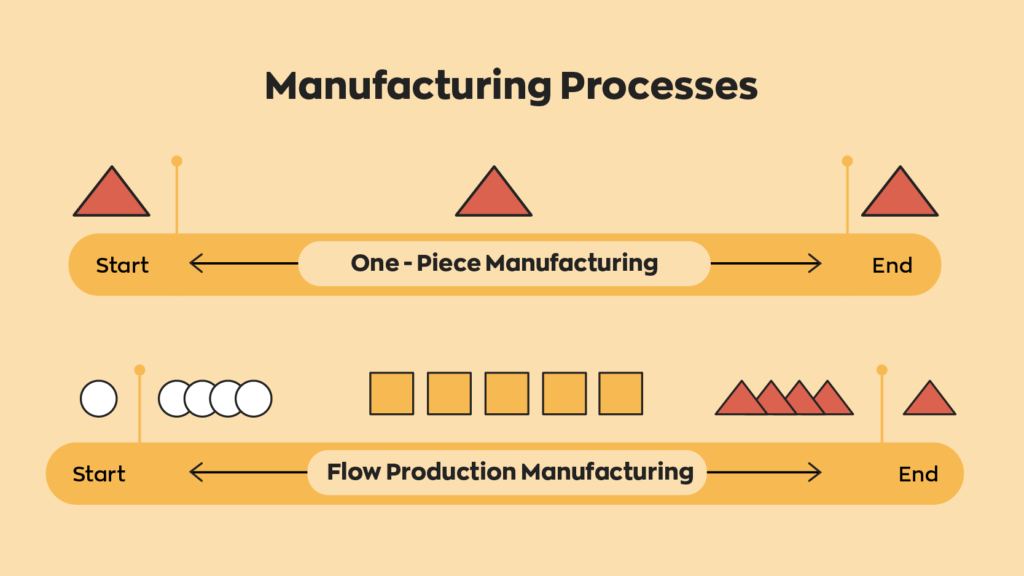
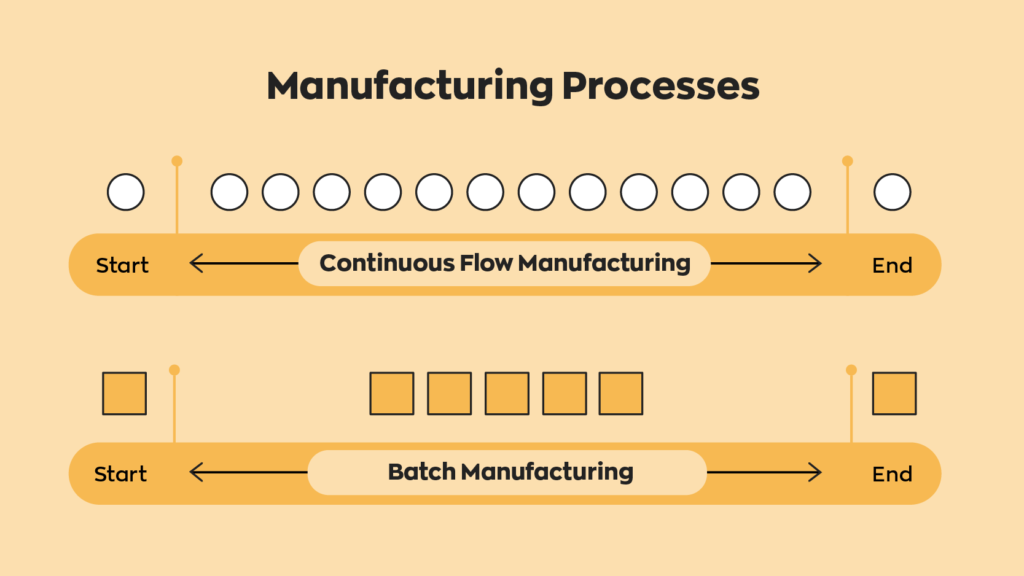
The scale of production is the most significant difference between these manufacturing processes. Instead of producing multiple units, one-piece flow focuses on producing a single unit at a time. Like anything, this has both pros and cons.
What are the benefits of one-piece flow?
A good way to summarize the benefits of one-piece flow is “quality over quantity.” Instead of multiple units at once, this manufacturing process prioritizes producing higher-quality products in exchange for smaller production yields. Here’s a more in-depth analysis:
The one-by-one nature of one-piece flow allows for greater control over the manufacturing process. Because only one unit is on the production line at any time, keeping track of things is more manageable. This also means that it’s not as disruptive if something goes wrong. You can easily pull something off the supply line without causing a bottleneck.
Because there’s only one product on the line at once, single-piece flow also reduces the amount of necessary inventory. This helps businesses save in a few ways. For starters, it reduces the materials they need to keep on hand and the warehouse space they need.
Last but certainly not least, one-piece flow generally increases the quality of products. This is a result of the greater control over the manufacturing process. Because only one unit is under production at a time, there’s more time to catch– and fix– any issues.
What about drawbacks?
Keep in mind that one-piece flow is only for some businesses. It’s a specialized process, and for this reason, only specific industries can really make use of it. While it has its benefits, the drawbacks are severe enough that they can cripple unprepared or unsuited businesses.
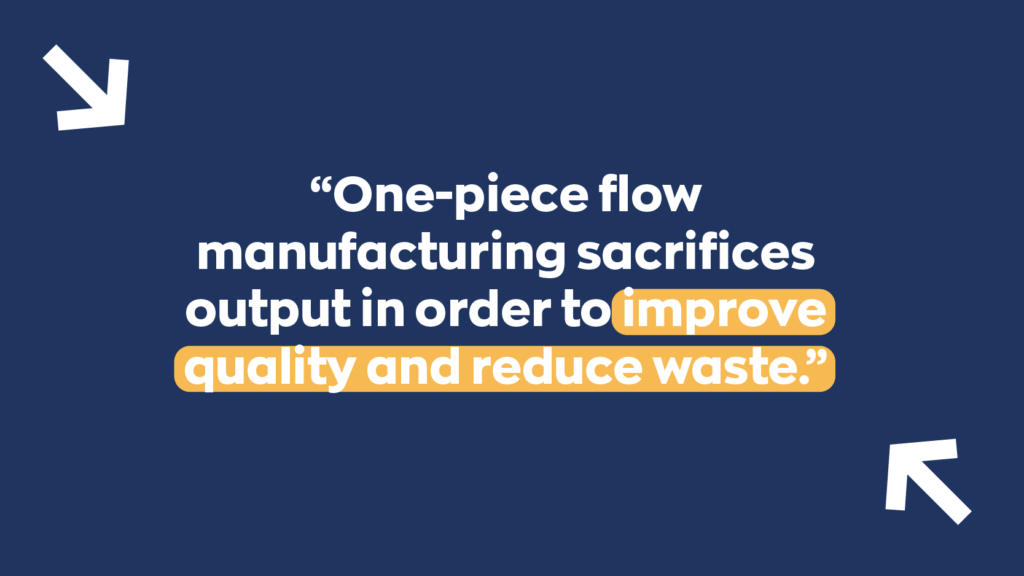
By far, the biggest drawback of one-piece flow is the lower yield. Manufacturing products one by one naturally means that your production yield will be lower. This decreases cash flow. Single-piece flow also means that your products will be in the work-in-progress stage more often than usual. While this might not seem like a big deal, it can make it difficult to calculate the manufacturing cost.
And while single-piece flow increases flexibility for a specific product, producing a variety of different products is difficult. This can hinder overall production output if your business makes a lot of product variants.
Implementing single-piece flow can also be challenging. Changing existing production lines is expensive, time-consuming, and takes time to adjust. It also requires data that takes time to gather.
When should you use one-piece flow manufacturing?
If you’re thinking about implementing one-piece flow, the most important thing to consider is the product you’re manufacturing. Generally, it’s best suited for products with a high individual unit value. For example, it makes more sense to use one-piece flow if you produce cars rather than loaves of bread.
That example may seem strange (and it is), but it also illustrates another point: scale. While vehicles are a part of our everyday life, food is purchased much more often. Because of this, a bakery profits by selling many loaves of bread. A car dealership, on the other hand, profits by selling low-volume high-price products.
Businesses that deal in custom products also tend to benefit from single-piece flow. Because the final product depends on the customer’s input, there’s no point in beginning production until an order comes in. It makes more sense to wait for an order to arrive and build to meet the customer’s specifications.
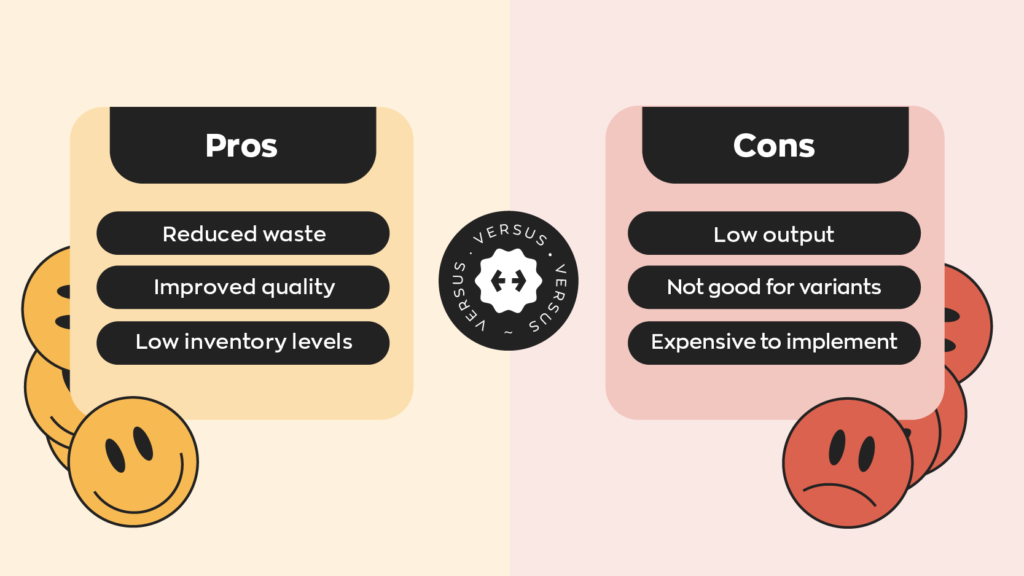
In short, while one-piece flow offers a number of benefits, only some businesses need those benefits. Furthermore, the drawbacks can be difficult to deal with. If you are thinking about implementing one-piece flow, ensure it’s something you genuinely need.
Manufacturing inventory software can help
Which manufacturing process you decide on varies from business to business. Software, on the other hand, is constant across the board. With software like inFlow, you can create work orders, generate a bill of materials, and track inventory. Our software can even help you calculate your cost of goods sold!
So, no matter which manufacturing process you decide is best for your business inFlow can help.
0 Comments