Key takeaways
- There are six main types of manufacturing processes: repetitive, discrete, job shop, continuous, batch, and 3D printing.
- Repetitive and Continuous processes are suited for high-volume, standardized products.
- Discrete and Job Shop allows for more customization and work well with varying product specifications.
- Batch manufacturing is flexible, allowing adjustments for product variations.
- 3D Printing enables highly customized, small-batch production.
- The manufacturing process you choose should be based on product requirements. You should consider factors like materials, budget, waste, product size, customization, and forecasted demand.
- Combining manufacturing processes for certain products can optimize your workflow and help you meet specific production goals.
Manufacturing methods are constantly evolving. Today, the industry reaches far and wide, with a vast range of types and subtypes of manufacturing, as well as different manufacturing software solutions and processes to support them. But no matter which area your business falls under, you’ll need to adopt one of the 6 types of manufacturing processes.
What is a manufacturing process?
Manufacturing processes are how we turn raw materials into a finished product. That product might be stand-alone or a component for something else.
A manufacturing process starts at the design stage, relying on the use of automated machinery, human experts, or both to build the goods.
Because many industries rely on efficient manufacturing, several processes have been developed to suit various needs. These fall into six categories.
What are the 6 types of manufacturing processes?
The six types of manufacturing processes differ in how they deal with a product’s journey from start to finish.
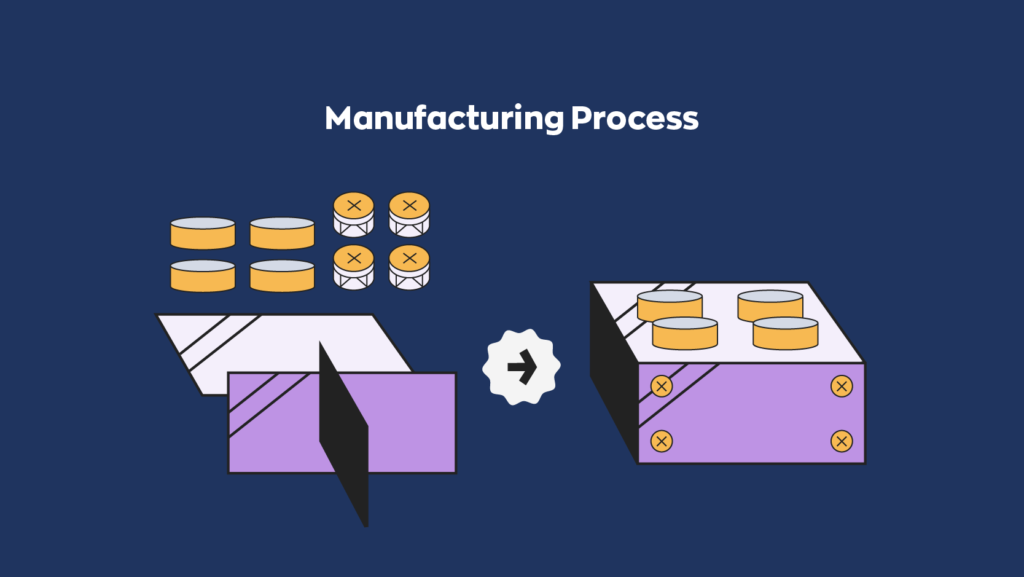
For example, in some processes, every product undergoes more or less the same journey, with set stages and parameters. Other processes work a little differently, treating products as individual items and allowing for customization.
Here are the six manufacturing processes (in no particular order):
- Repetitive manufacturing
- Discrete manufacturing
- Job shop manufacturing
- Continuous process manufacturing
- Batch process manufacturing
- 3D printing
Until recent years, manufacturing processes were broken down into five categories rather than six. This is because 3D printing uses modern technology, and its uses are still being developed today (more on this below).
What do these manufacturing processes involve?
1. Repetitive manufacturing
Repetitive manufacturing does exactly what it says, makes goods by following repetitive steps. This is ideal for consistent, high-volume production with few variations. The production line can run almost constantly if needed.
However, there is one significant disadvantage. If there is a fault with any part of the production, all other areas and all items will be affected, unlike in manufacturing processes with more variation
2. Discrete manufacturing
In discrete manufacturing, you view products as individual items. So, the steps have more changes than on a repetitive production line. This is beneficial for manufacturers producing a range of items, perhaps with changes in size or style. Car manufacturers might use this method.
The various products may or may not be very different from each other. But the more changes there are, the more time needed to set up the production line each time.
3. Job shop manufacturing
Job shop manufacturing has been described as the “ultimate case of discrete manufacturing.” This is because it treats each item as unique, allowing for customized details.
This type of manufacturing process usually involves production areas or workstations rather than lines and is applied to small-quantity or individual orders. Job shop setups are often associated with just-in-time approaches to manufacturing when you make products as needed rather than in advance.
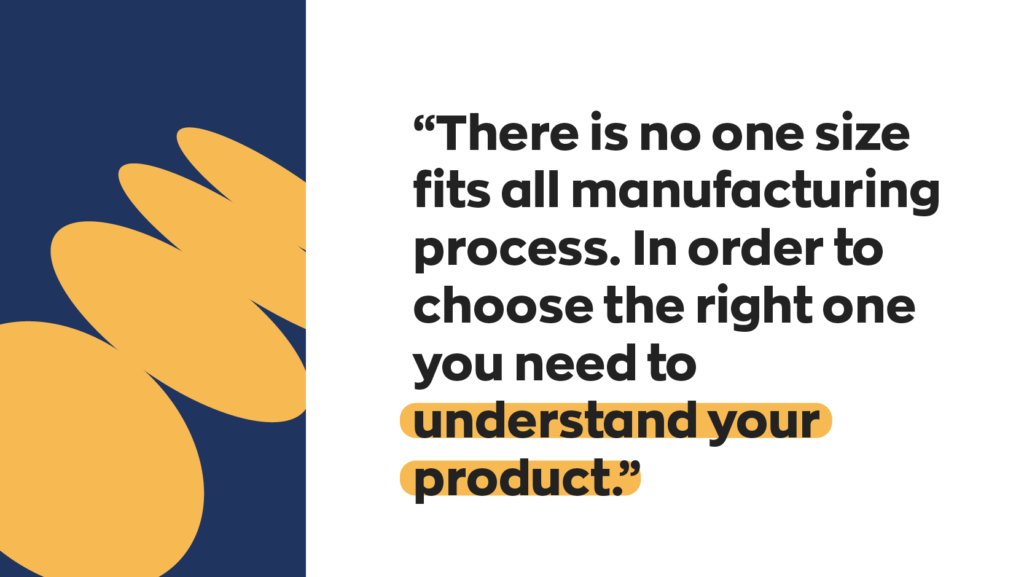
4. Continuous process manufacturing
In continuous manufacturing, materials constantly move through the production line, just like in repetitive manufacturing.
The main difference here is that continuous manufacturing generally uses raw materials that undergo some kind of chemical reaction or change. So, the process is a continuous flow.
5. Batch process manufacturing
Batch manufacturing treats products as a group. When all the goods from one batch have finished a particular stage, they move on together. Every finished product from one batch should be identical.
We tend to use batch manufacturing processes when we need flexibility. For example, we can change a batch’s size or customize a stage to add a design feature.
Because the products in a batch need to be the same, a lot of the work can be done by machines, with workers overseeing the process.
6. 3D printing
3D printing, sometimes called additive manufacturing, is one of the newest types of manufacturing to become popular. The process often starts with scanning an object or creating a 3D design on CAD software. A machine would then join materials layer by layer to create a physical version.
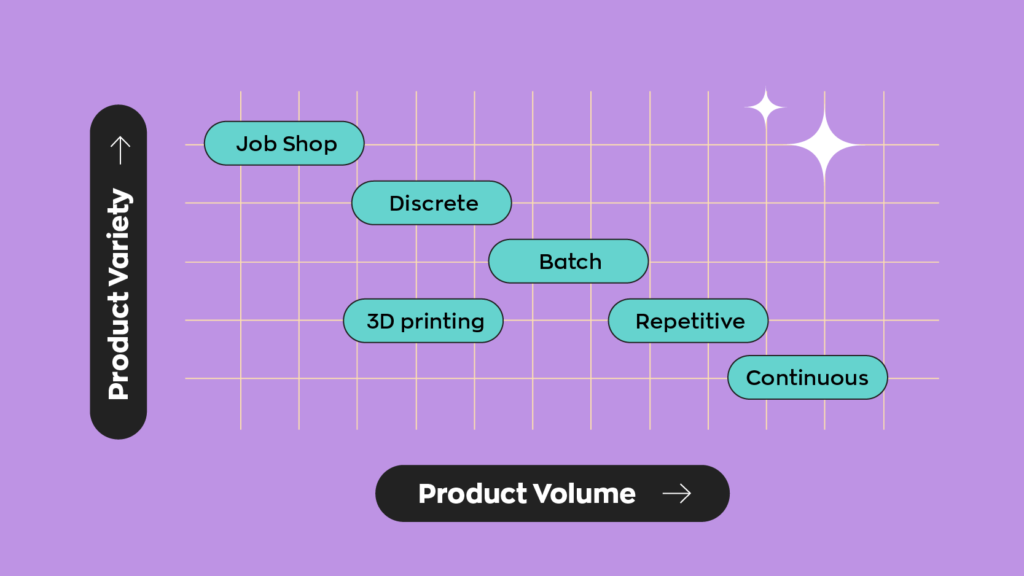
Guinness World Records says that the first patent for a 3D printer “was filed on 12 July 1967 in Denmark by Wyn Kelly Swainson, a 27-year-old American graduate student.” The student studied English literature and wanted to find a way to make 3D copies of sculptures in the same way we can take photographs of paintings.
Recently, 3D printing hit the news when companies started to print visors for frontline staff during the pandemic. From established manufacturers to hobbyists, people with access to 3D printers banded together to produce the protective equipment.
Choosing a manufacturing method
There is no one “right” manufacturing method. What works best for each business depends on a wide range of factors, most of which relate to the product or operational costs. These include, amongst others:
- Materials & Components – The raw materials you are working with will play a huge factor in your manufacturing process. For example, if you’re dealing with perishables, you will probably want to go with batch manufacturing; that way, you can assign batch and lot numbers to the products you’re manufacturing.
- Budget – Depending on your available cash flow, you may want to avoid some manufacturing processes that tend to be more costly, such as job shop manufacturing.
- Length of Phases – Varying phase lengths can cause severe bottlenecks in the production process. This is why it’s best to avoid repetitive or continuous manufacturing in these cases and explore other manufacturing processes instead.
- Wastage – Different manufacturing processes will naturally result in a different amount of waste. If your products consist of expensive components, avoid the high waste-producing processes.
- Volume of Products – If you’re looking to create products in high volume, you should consider a high-producing process such as continuous or repetitive manufacturing.
- Product Dimensions – Believe it or not, even the size of the products you’re creating will play a role in which manufacturing process is right for you. You’ll need to look into the size of your facility and the machinery you’ll be using to assemble your products.
To get a better understanding, take a look at the examples below.
Examples of manufacturing methods
Let’s imagine Mark, an amateur baker, makes the tastiest cupcakes in town and decides it’s time to go pro. So, what’s the best manufacturing method for him?
First, you’ve probably heard of batch baking. In batch baking, Mark would make a set number of identical cupcakes at once. This is a good option if he wants to sell several flavors of cupcakes in his own bakery. Working in batches usually means there isn’t a lot of set-up time when switching between products. He could also scale up or down the quantities of certain flavors as needed.
On the other hand, Mark might win a fantastic contract and find himself supplying his best-selling cupcake to supermarkets far and wide. In that case, Mark will need large-scale production for one item. A repetitive manufacturing process would allow him to meet targets by streamlining each stage and ensuring there are no production breaks.
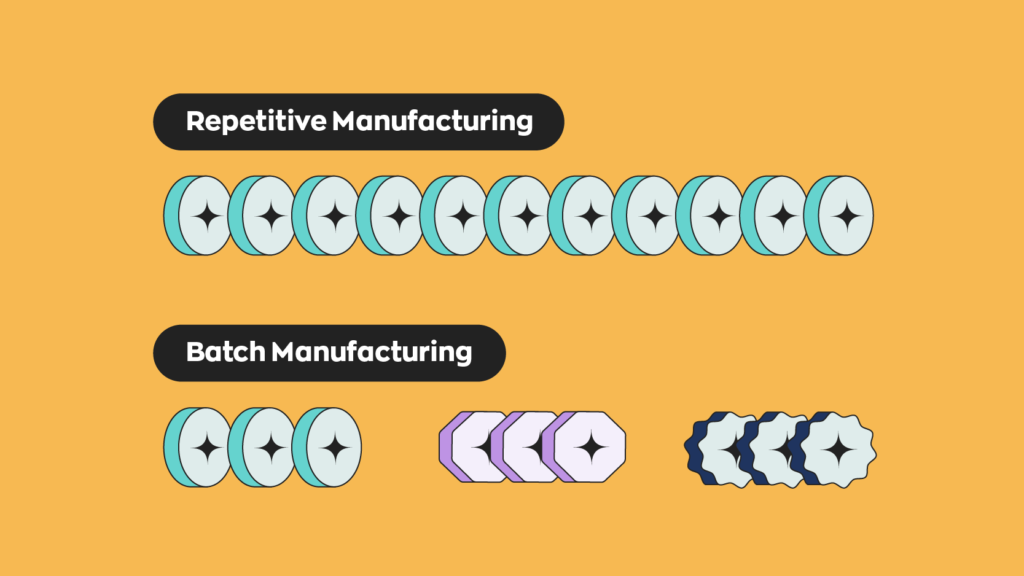
Or he could combine the methods and make the dough in batches but bake on a continuous conveyer belt.
When choosing a manufacturing method, it’s essential to do in-depth research, talk to experts, and consider what works best for your business, not just your competitors.
Managing inventory for manufacturing processes
Whatever manufacturing methods and processes you choose, staying on top of inventory is important. This means knowing what you have, where it is, how to access it, and when you might need more.
Software like inFlow has assembly and BOM features, reducing manual checks by updating inventory in real time. That way, you know exactly what you have in stock and how much you can make.
0 Comments