Key Takeaways
- Physical inventory counts are crucial for maintaining accurate inventory and avoiding potential issues like excess inventory or stockouts.
- Count sheets help streamline the cycle count process.
- Proper preparation is key to a smooth inventory count, including shutting down operations and/or organizing the warehouse into sections for efficient counting.
- Tools required for a physical count are minimal: count sheets, a pen or pencil, and a printer.
[Note: If you already use inFlow, we’d recommend reading our cycle count workflow instead.]
The physical inventory count sheet is the most straightforward part of a physical count. You’ll first want to download our inFlow Count Sheet template to get everything started.
This spreadsheet will help you count all of the products in your storage location or warehouse to ensure that your records reflect what you have on hand. There are several reasons that records can go astray over time. For example, stock adjustments might have mistakes, purchase orders could be placed in the wrong location, and items could break or be stolen.
Doing a physical inventory count is an essential part of ensuring the accuracy of your inventory system. The fact is inventory counts are just as important as buying and selling new products. You could run into major issues if your counts stray too far from reality over time. Some of these include being unable to fulfill a big order for an important customer or over-ordering new stock when you still have plenty left over.
Count sheets are also helpful because they can create a snapshot of your inventory levels for a particular date. This can be useful for later comparisons. For instance, you could compare how much stock you had left at the end of last quarter versus this quarter.
How often you do these counts is up to you and your business. Larger shops can defer physical inventory counts for up to a year because of the amount of preparation and work required to execute a count properly. However, consider doing counts every three to six months to ensure your inventory’s accuracy.
What you need to perform a physical inventory count
The good news is to perform a physical inventory count, you won’t need much. First and foremost, you’ll need a count sheet (you can download the attached inventory count sheet template above). Next, you’ll need a pen or pencil, and lastly, you’ll need a printer and paper in order to print out your count sheets.
It’s safe to say that you probably have all the required supplies and tools necessary for a physical inventory count, so the real work comes in the preparation. This step should be considered carefully to ensure that your inventory count goes as smoothly as possible.
How do we prepare for a physical count?
The biggest obstacle in preparing for a physical count is finding the right time to do it. In order for the count to be accurate, you’ll need to shut down your operations. This means no stock goes in and out of your storage area or warehouse. Be sure to close out any pending sales orders and ensure not to accept new stock on incoming purchase orders until the count is done. The end of a standard business day, or even the end of a week, is a pretty good time to start a count. Some businesses will run complete inventory counts overnight so the warehouse is up and running by the time the store opens the next day.
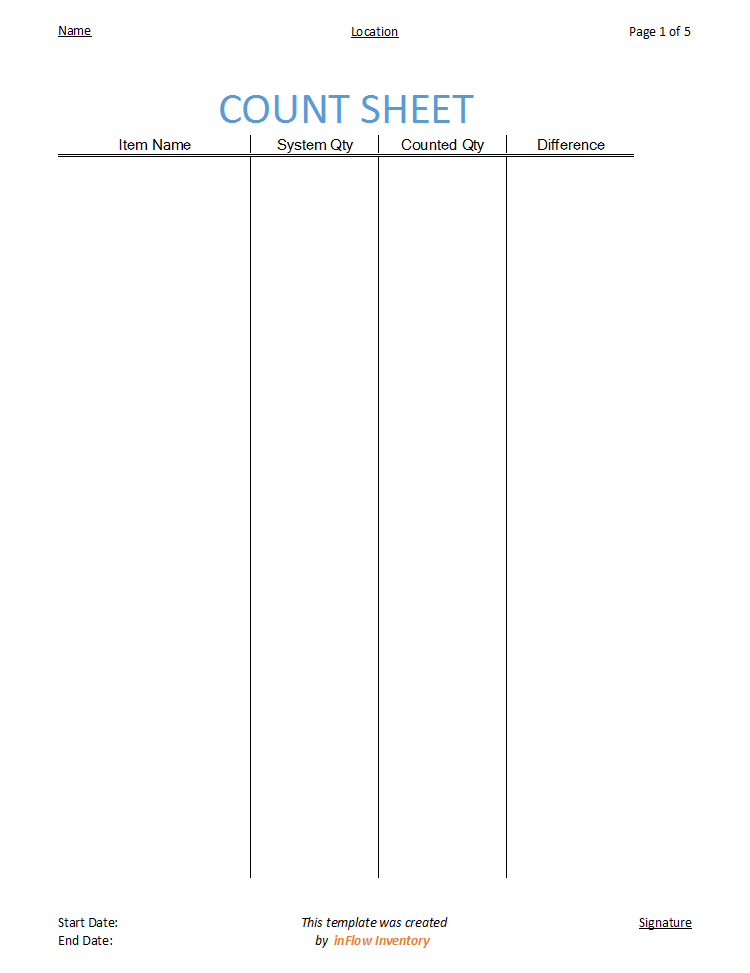
Depending on the size of your storage area, you can also create one inventory count sheet per section. You can divide a warehouse into aisles or lots and send specific people to count the items in those areas. This kind of division of labor can make the whole process much faster since you can count multiple areas of the warehouse simultaneously without the fear of double counting.
Printing and using the count sheet template
In order to use the inFlow Count Sheet template, you’ll want to make sure you fill out these fields:
- Decide which area of the warehouse the current inventory count sheet will correspond to. Place this info into the “Location” field at the top.
- Pull the item names from your product list and paste them into the “Item Name/SKU” column. Then paste the current quantities (according to your records) into the “Recorded Qty” column.
- Print the count sheet out and make sure all pages print correctly.
- Fill out the name of the person assigned to this section in the “Name” field.
- Write the current date into the Start Date field in the footer. This will help record-keeping in the future, so you’ll know what day this inventory count sheet was from.
- The person performing the physical inventory count (the “Name” from step four) can now begin the inventory count. It’s essential that they count each section of the storage area or warehouse one at a time to reduce errors. The person performing the count should place the final tallies for each product in the Counted Qty column.
- When you finish the physical inventory count, you can calculate the “Difference” column by subtracting the Counted Qty from the Recorded Qty.
- You’ll also want whoever is in charge to sign the footer and record the End date.
Once you finalize all values on the inventory count sheet, you can return to your master stock list and adjust your records according to the Counted Qty from the sheets. This will ensure that your records align with your actual inventory levels, as well as the inventory levels stored in your warehouse management software system.
inFlow simplifies inventory count sheets when it counts
If you want to make this process even more efficient, create your count sheets in inFlow. The Recorded Qty can be pre-filled for you since inFlow tracks your current stock levels and calculates the differences automatically.
INVENTORY COUNT